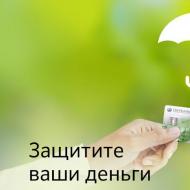
How to find the production cost of commercial products. The cost of realized products: formula, technique and calculation example
The article is various approaches to the calculation of cost, formulas, ways to classify the costs used in calculation. In addition, we led an example of calculating the cost of production in production.
In this article you will learn:
Before making the calculation of the cost of products, the financial director must be answered by the following questions:
- the cost of which accounting object must be determined (manufactured products, technological process, separate order);
- what costs will be included (calculating the full or truncated costing (Direct Costing);
- based on what data will be made (regulatory or actual);
- how to distribute indirect costs and take into account them.
Cost classification
The classification depends on which management task it is necessary to solve, for example, to calculate the cost or profits from its implementation, assess the results of the responsibility center.
By way of inclusionthey are divided into direct and indirect. Direct can be accurately and only in the cost of the product being produced or another calculation object. As a rule, they include costs of raw materials and materials used for the production of products, as well as expenses for the labor of the main production personnel, which are taken into account in the account 20 "Basic Production".
It is impossible to be economically reasonable to associate with a specific accounting object. These include overall, general and commercial costs. They relate to the calculation object by distribution in accordance with the method adopted at the enterprise and the distribution base.
In relation to the volume of production Costs can be .
Variables depend on the volume of production or sales, and in terms of a unit of products remain unchanged (raw materials and materials, piecework wages of production workers, electricity).
Permanents do not change with an increase in production (rental of premises, equipment for the release of one type of product, the wages of the administration), but calculated per unit of products - are adjusted with a change in the level of business activity. It should be noted that permanent and variable costs with direct and indirect should not be confused (see Table 1).
Significance for a specific solutionall expenses can be divided into relevant and irrelevant. Irrelevant - these are the costs that do not depend on received. For example, an enterprise has a building. Two options for using it are considered: Create a sewing shop or use under the warehouse. In this case, the cost of maintaining the building and utilities They will be irrelevant, as they do not depend on the decision. Costs associated with the creation of a workshop or retrofitting of premises for use under the warehouse, on the contrary, relevant.
It should be noted that such a classification occurs quite rarely. Most enterprises all major types of production costs are recognized relevant and take into account when analyzing cost finished products.
How to group costs in order to more accurately attribute them to the cost
Assumptions made in calculating costs, when all indirect costs are distributed proportional to a single base, lead to serious distortions and threaten the financial well-being of the enterprise. More precisely, it is possible to calculate the cost of products if you use your unique diversity of indirect costs for each group of spending. But for this it is very important to correctly allocate the costs of costs. See how to do it.
Table 1. Example of permanent, variables, direct and indirect expenses
Expenses |
Permanent |
Variables |
Salary of engineering and technical workers, depreciation of equipment in manufacturing units |
Salary of the main production workers, raw materials and materials, sales commission, electricity consumption in production |
|
Indirect |
Salary of leadership and managers, salary of sales representatives, heating, depreciation of equipment in the auxiliary units |
Electricity for auxiliary units, fuel expenditures for sales department |
Methods of calculation
In practice, various approaches to the formation of cost (Classification of methods, see Figure). The use of one or another approach is determined by the peculiarities of the production process, the nature of the manufactured products or services provided and other factors.
Picture.
Completeness of the cost. It is possible to determine both the complete and truncated cost of products. Complete (absorption costing) is calculated taking into account all expenses incurred by the company.
Complete cost
Truncated (Direct Costing) assumes that only variable costs include the cost of products. Constant of the general production, as well as commercial and general running costs Disposable to reduce revenue at the end of the reporting period without distribution to released products.
The cost calculation formula will look like this:
The cost of realized products \u003d variable costs for units. × Sales of implementation
The calculation by the method of direct-cobing is justified in cases where it is necessary to decide on the release or termination of the production of a product.
Truncated
When using the ABSORPTION COSTING method, the cost of the unit of products includes both variables and constant costs. The method is justified when necessary to analyze, form an optimal product range or develop a price policy on the principle of "costs plus". In other words, the price is defined as a complete cost, increased by the desired profitability.
Formulas will look like this:
Cost unit product \u003d variable costs for units. + Permanent / production
The cost of realized products \u003d cost of units. × Sales of implementation
Compare two approaches
The financial results of the company, calculated using the Direct Costing method, may differ from the results obtained using the Complementability method.
Let us give an example.
The company during the reporting period produced 1500 units of products. Variable costs for the production of a unit of products are 50 rubles. The total amount of permanent costs is 30,000 rubles. Sales volume - 1000 units of products at a price of 100 rubles. for a unit. At the beginning of the period of reserves of unfinished production and finished products were absent. Calculation by the method of complete and truncated cost is presented in Table. 2.
As can be seen from the example, the result financial activities In the case of the application of various calculation methods, it will be different due to the fact that at the end of the reporting period in the company formed a stock of finished products in the amount of 500 units. In other words, if the level of stocks at the end of the year will increase, financial resultsdefined on the basis of complete cost will be higher than if it was designed to use direct-cob. When reducing the level of stocks, the picture will be inverse: when using a truncated cost profit will be more.
Table 2. Comparison of approaches to calculation
Indicators |
Direct Costing method (truncated) |
ABSORPTION COSTING (ABSORPTION COSTING) |
||
Formula of calculation |
Value, rub. |
Formula of calculation |
Value, rub. |
|
100 rubles. × 1000 units. (Price × sales volume) |
||||
Cost unit products |
50 rubles. + 30 000 rub. / 1500 units. (Variable cost per unit. + Permanent / production volume) |
|||
The cost of realized products |
50 rubles. × 1000 units. (Variable costs for units. × Sales of implementation) |
70 rubles. × 1000 units. (Cost of units. × Sales of implementation) |
||
100 000 rubles. - 50 000 rub. (Revenue from sales - the cost of realized products) |
||||
Permanent expenses |
||||
Operating profit |
50 000 rubles. - 30 000 rubles. (Marginal profit - permanent costs) |
100 000 rubles. - 70 000 rubles. (Revenue from sales - the cost of realized products) |
Actual and regulatory cost
Calculation can be made based on the actually incurred costs or on the basis of established raw materials and materials consumption norms, as well as regulatory costs of labor.
The use of regulatory cost allows you to control the efficiency of resource spending and respond timely to emerging deviations.
The actual cost can be defined only after all costs are reflected in the account. The main disadvantage of this method is considered rather low efficiency (data can be obtained only at the end of the order, manufacturing the product, etc.). In practice, both approaches are used.
Cost accounting objects
Depending on the calculation object, you can allocate
- marked
- poprocessory,
- calculation of the cost of individual functions (Activity based Costing, ABC).
The choice of this or that object of calculation affects the specifics of the business (stream production, small-sector, accounting for individual orders).
Browse method Applied in the manufacture, for example, unique equipment, when performing separate orders. Camely More characteristic of enterprises with serial and streaming production, when the product passes several steps of processing. In this case, the product of the calculation becomes the product of each redistribution (production stage). Poprocessive It is also characteristic of the objects of the extractive industry, but is also used in industries with an uncomplicated technological cycle (for example, in the production of asphalt).
For aBC method accounting costs Organized on individual functions, operations performed by the company's divisions. For example, the management of the autodiere enterprise intends to control the cost of functions - car sale in the commercial department or their maintenance in the service center. This may be necessary when making a decision on outsourcing individual business functions. In addition, ABC allows you to more accurately distribute indirect costs when calculating the full cost.
Quite often, the calculation methods are applied in combination. For example, a variant of the requested method of calculation with incomplete consideration of expenses or copulination using raw material consumption standards and materials or with regard to their actual consumption is possible.
One of the main problems associated with the calculation of the total cost of a unit of products is the need to distribute indirect expenses. The easiest way is the direct distribution of the cost of service units in proportion to a single base (the salary of the main production workers, the costs of raw materials and materials, man-clock). However, such an approach, as a rule, does not allow reliably and economically reasonable to distribute indirect costs, which means it may cause incorrect management decisions.
A multi-level distribution method performed in several stages is more accurate.
Step 1.All costs for the period are grouped by divisions. For example, the following expenses will be grouped according to the dining unit: the salary of dining personnel, food costs, the cost of electricity consumed, etc.
Step 2. The costs of auxiliary divisions are redistributed among production departments and workshops. For example, the cost of maintaining the dining room must be distributed into two industrial workshops. To do this, you need to choose a base: in the case of the dining room it will be advisable to distribute its spending in proportion to the number of operating in each workshop.
Step 3. Costs related to production units are distributed to released products. For example, after the cost of the dining room costs were redistributed into two workshops, the cost of the content of each workshop (the costs of the workshop + distributed costs of the auxiliary unit) relates to manufactured products. As a base for distribution, the number of human-hours, spent on the release of each type of product, the cost of raw materials and materials, etc.
Excel model for calculating cost
If you need to calculate the direct production cost of products, use the finished settlement model in Excel. See how to adapt the model under the characteristics of the company: Create reference books, adjust the methodology to attribute direct costs for the cost.
Calculation of the cost of products at the manufacturing plant: Example
Consider on the example of a large machine-building plant - JSC SSM-Tyazhmash, how the costs can be organized and the cost of production is calculated.
SSM-Tyazhmash OJSC is a subsidiary of OJSC Severstal, which specializes in the manufacture and repair of metallurgical equipment. A few years ago, a project for the implementation of the Axapta system was launched at the enterprise. At the same time, principles were developed management accounting and the formation of production costs. Prior to that, the cost of finished products was calculated for accounting and tax goals, and the administrative, with the necessary financial director of the analyst, was absent. Automated system "1C: Accounting" did not provide the required level of data detail.
Grouping costs
In the formation of the structure of production costs, direct expenses include the material costs and the cost of production services from third-party companies. All costs that will need to be distributed to calculation objects are combined into groups depending on the source of their occurrence (see Table 3).
The company is calculated by a complete production cost, while the magnitude of indirect costs in its structure can reach 40-60%.
The cost carrier (calculation object) is a production order, in the foundry of production, accounting is also carried out by redistribution.
Table 3.. The structure of the production cost of JSC SSM-Tyazmash
Group |
Account analytics |
Source source |
Primary accounting documents |
Straight |
|||
Materials |
Nomenclature |
Consumption of raw materials and materials, semi-finished products specified in the specification for finished products and semi-finished products |
Acts of write-off materials in production |
Provider |
Providing production services by third-party providers with the direct inclusion of these costs in the relevant production orders |
Accounts received from suppliers; Acts of work performed |
|
Indirect |
|||
General production expenses |
Staff |
All of the general production costs collected in the account 25 "general production costs", both depending on the enterprise (depreciation of the OS, FOTS workers), as well as caused by external factors (water suppliers, heat suppliers, etc.) |
Consolidated wage statements, acts at the services of third-party organizations, etc. |
Auxiliary materials |
Nomenclature |
All expenses due to write-off on technological needs on a nomenclature relating to subsidiary materials (also taken into account on account 25 "general production costs") |
Acts of write-off, for example, to the repair fund, on labor protection, on the mainstream maintenance |
Intercepted cooperation |
HZZ. |
Costs caused by the fact that the sites of workshops provide services to each other. Are distributed between the customers divisions in proportion to the time actually spent on the execution of their orders |
Swelling overhead, order cards, etc. |
Attribution to the cost of direct costs
The initial stage of calculation is the attribution of direct costs for production orders. As a rule, this is not difficult: in accordance with the specification on the types of finished products and semi-finished products, raw materials and materials are written off on specific orders in the analytics of species of costs and the IVZ.
Distribution of indirect expenses
The methodology for the distribution of all-generating costs and attributes them to the cost of production includes several stages that we will consider in more detail.
Collection of general industrial costs. Their sums are taken into account on account 25 in the analytics of costs and the cost center (production sites of workshops and non-production units of the enterprise). At the same account, all expenses for auxiliary materials are collected and groups of costs and the IWZ are assembled. An example of accounting economic operations The code is shown in Table. four.
Table 4.. Grouping collected costs by types and places of their occurrence
date |
Name |
Amount, rub. |
Plot code (MWZ) |
|
Other auxiliary materials |
||||
Materials for labor protection |
||||
Other gsm |
||||
Energy on technology |
Code structure.The code consists of seven characters. Consider code 008-02-05 "Other fuel". The first three digits (008) - the cost of the cost group "The content of fixed assets", the following two (02) - the code of the subgroup "fuel and fuels", the last (05) - the sequence number inside the subgroup. Thus, based on the code, one can uniquely conclude that this type of expenses is related to which group and subgroup.
The codes of the MWZ are formed according to the following principle. The first three digits are the code of the workshop. For example, 020 01-03, where the code of the workshop 020 "The shaped foundry shop - FLC" says that these are the main production sites of the workshop, 03 - the sequence number of the site inside the workshop (in this case - Plot of smelting cast iron).
Distribution of collected costs of production orders. The distribution base for orders collected by the general production costs, including associated with the use of auxiliary materials, can be human-clock, norm-clock, machine-hours, conditional tons, tons of surfacing, etc., that is, natural indicators.
To connect the operations performed with the IMP and the types of costs, it is necessary to proceed from the following:
- with any technological operation made as part of the order, a list of expenses, the amounts of which must be attributed to the order;
- any technological operation must be associated with a specific area of \u200b\u200bthe production workshop. For example, the operation of the machine-drawing can be performed at the machine section of the repair and mechanical workshop or on the preparation site for the production of the assembly shop. The cost of these operations will differ.
Collecting total costs of intercity cooperation. All expenses (and straight, and indirect distributed) are assembled on the basis. primary documents In terms of production orders made within the framework of intercepted cooperation. At the same time, the total operating time of each executive unit for the Customer's division in the period under consideration is summed up. The costs of intercepted cooperation are grouped at the places of their occurrence and in the same type - "The total costs of interstitial cooperation".
Distribution of costs for intercuring cooperation for production orders. Within the framework of individual orders, work is performed (services) providing the manufacture of a finite finite product. At the same time, all expenses incurred within such "related orders" must be included in the cost of the finished product. In other words, they are redistributed between production orders, and not sites of workshops.
Final calculation of production orders. All costs collected within the framework of production orders are summed by calculating the final cost.
Consider an example of calculation at the production of JSC SSM-Tyazmash. IN reporting period Three orders were completed - order 1, order 2, order 3. Direct costs for them were 100, 200, 150 rubles, respectively And they were immediately written off on completed orders.
Orders were performed by two production sites (section 1 and section 2). In addition, the service site was involved, which in the current month provided equipment repair services to the main plots. To simplify the calculations on intercepted cooperation, suppose that the main plots did not provide services to each other, as well as the serving site.
Collection of the cost of the 1st and 2nd production sites. Plot 1 worked 50 norms-hour, its costs amounted to 500 rubles, thus the cost of the norm-hour is equal to 10 rubles.
Plot 2 worked 20 cars, total amount Costs amounted to 800 rubles, the cost of machine-shift - 40 rubles.
Collecting the cost of the service section. According to the service area, the volume of production amounted to 30 people-hour., The total amount of costs for current period - 150 rubles., The actual cost of man-hour - 5 rubles.
Distribution of the cost of the service section for production sites 1 and 2. For a plot 1, the serving site worked 10 people-hour., For a plot of 2 - 20 people-hour. Working hours for production workshops will be used as the database of the distribution of expenses of the serving site in the amount of 150 rubles.
Thus, 50 rubles is additionally distributed to the site 1. (10 people -Hh. × 150 rubles / 30 people-hour.), On the plot 2 - 100 rubles. (20 people-hour. × 150 rubles / 30 people-hour.). As a result, the costs of the section 1 will develop from our own costs of this area in the amount of 500 rubles. and redistributed from the service site in the amount of 50 rubles. By section 2, the same: 800 and 100 rubles.
Redistribution of costs of production sites for completed orders. Plot 1 worked 30 norms-hour. to execute order 2; 20 norms-hour. To order 3. Hence, the cost of 300 rubles will be attributed to the second order. (500 × 30/50), on the execution of the third order - 200 rubles. (500 × 20/50).
Plot 2 worked on completing order 1 and order 3 to 10 machine-shift. Accordingly, each of these orders will be attributed to its costs in the amount of 400 rubles. (800 × 10/20).
Redistribution of costs of intercuring cooperation for orders. As a result of the distribution of the costs of the serving site to the site 1 we received 50 rubles. With the volume of production of a plot of 1 to 50 moph. The cost of one norm-hour will be 1 rub. By analogy in the section 2, it will be 5 rubles. (100/20).
Accordingly, the cost of order 1 will add 50 rubles. From site 2 (5 rubles. × 10 Machine-shift), order 2 - 30 rubles. (1 rub. × 30 normo-hour.) From the plot 1, order 3 - 20 rubles. From section 1 (1 rub. × 20 normo-hour.) And 50 rubles. From site 2 (5 rubles. × 10 Machine-shift). Imagine the results of the distribution of costs in Table. five.
Table 5. Complete calculation of orders made, rub.
Completed orders |
Expenses |
Total cost |
||||
Straight |
Plot 1. |
Plot 2. |
Distributed maintenance costs |
|||
plot 1. |
plot 2. |
|||||
From this article you will learn:
- What includes the calculation of the actual cost of finished products
The calculation of the cost of finished products is necessary in various situations, including for pricing. It is extreme an important indicator. It reflects the total financial costs for the manufacture of the product. On its basis, the optimal finite price of the goods is calculated. Analysis of production costs is needed so that the company does not incur damages due to overestimated prices. Consider the methods for calculating the cost and the expenditure items that need to be taken into account to obtain a realistic result.
At what stage is to calculate the cost of finished products
To create a successful enterprise, it is not enough to choose a direction and come up with an idea. The main thing is to make a reasonable business plan with the calculation of all expenses and expected revenues. As soon as clarity has been achieved in these indicators, you can proceed to its implementation.
The bulk of the cost is the cost of finished products, to calculate which you need to have special knowledge and skills. Calculation of the cost is necessary and current business, especially when optimizing costs (after all, you need to know their composition and structure, to understand what they affect). Different companies and expenses will be different. All costs are united in articles, but not every kind of effect affects the cost of finished products, and it is necessary to determine in each case individually.
Depending on the range of expenses, three types of costs are isolated: full, incomplete workshop and industrial. But it is not at all that they will all be involved in the calculations. Each businessman independently decides what costs and other indicators include in their analysis. For example, in the calculation of taxes, the cost of finished products is not involved, as they do not depend on it.
However, the cost of goods should be reflected in accounting reports, therefore, all costs that affect it should be included in the company's accounting policies.
It is possible to calculate both the total cost of production and the cost of one specific category of goods. In the second case, the value will need to be divided into the number of units of finished products to determine the cost of one product.
How to calculate the cost of finished products
To release one copy of the goods, the company will have to spend some amount of money on raw materials, equipment, consumables, fuel and other types of energy, taxes, pay for the work of workers and incur some costs associated with the sale of finished products. The sum of these costs is the cost of the unit of the product.
In practice, there are two ways to calculate the cost of finished products for the purposes of production planning and the calculation of the finished car mass:
- Calculation of the cost of the entire mass of products by economic elements costs.
- Calculation of the cost of one unit of goods through calculation articles of expenses.
All the money spent by the production company (until the placement of the batch of finished products to the warehouse) makes up a clean factory cost. However, it does not include the sale of goods that should also be considered. Therefore, the total cost of finished products also includes the cost of loading and delivery to the customer - the salary of movers, rental of the crane, transportation costs.
Calculation of cost shows how much money went directly to the manufacture of goods in the workshop, and how much - on its transportation after exiting the factory. The obtained costs will be used in the future, at other stages of accounting and analysis of costs.
In total, there are several types of product costs:
- shop;
- manufacturing;
- full;
- individual;
- middle-grade.
After calculating each of them, we obtain material for analyzing all stages of the production cycle, which will help, for example, to find opportunities to reduce the cost of release without losing the quality of the goods.
To calculate the cost of the unit of finished products, all costs are combined into articles. Indicators for each heading are recorded in the table and summarize.
Calculation of the cost of finished products taking into account costs
The sectoral production specificity strongly affects the structure of the cost of finite goods or services. Each industry has its own prevailing articles of production costs. It is for them that it is necessary to pay special attention when finding ways to reduce costs and increase profitability.
Each type of costs present in the calculations corresponds to its percentage, showing, is this type of cost priority or additional. All costs grouped by articles form the cost structure, and their position reflect a share in the total amount.
The share occupied by one or another type of costs in the total amount of expenses affect:
- place of production;
- application of innovation;
- inflation rate in the country;
- concentration of production;
- changing value interest rate on loans;
- other factors.
Obviously, the cost of the cost of finished products will constantly change, even if you release the same product for many years in a row. This indicator needs to be carefully monitored, otherwise the company can go bankrupt. Analyze the cost and promptly reduce production costs with the help of estimating the costs listed in the calculation articles.
Typically, companies use a calculation method for calculating the cost of finished products, semi-finished products or services. This is a calculation on the commodity unit manufactured at an industrial enterprise (for example, the cost of supplying one kW / h of electricity, one ton of metal rolling, one m / km of cargo transportation). For a calculation, a standard unit of measurement is taken in physical terms.
For the release of products, raw materials and additional materials, equipment, the work of the service personnel, managers and other employees are necessary. Therefore, various expenses can be used in the calculations. For example, it is possible to calculate the workshop cost of production on the basis of direct costs, the remaining indicators will not be involved in the analysis.
To begin with, all existing expenses are grouped by similar features, which makes it possible to accurately determine the amount of production costs on one economic component. You can group them in such parameters as:
The purpose of the classification of costs of cost-based costs based on common features is to identify specific objects or a place where costs arise.
A grouping based on economic homogeneity is carried out in order to calculate the total costs per unit of products produced, which are folded from:
This list of economic elements is one for all industrial sectors and is used everywhere, so we have the opportunity to compare the cost structure of goods by various enterprises.
Calculation of the actual cost of finished products
To profitably sell your products, it is necessary to accurately determine their cost. Finished products are the goods that have passed all the stages of technological processing and control checks (the remaining refer to incomplete production).
Calculate the actual cost of the product by two methods. In order to use the first, you need:
- take into account all direct expenses and other costs;
- rate goods.
Instructions in the first way:
- Finished products are part of the material and reserves intended for sale, and is reflected in the score 43 with the characteristic name. It can be estimated on the basis of the cost - planned manufacturing or actual.
As the costs included in the cost of finished products, absolutely all expenses constituting the production cost of goods, or only direct costs (this is relevant when indirect is debited from account 26 to account 90).
- In practice, few people form the price of the goods based on its actual production cost. This calculation method practices small companies that produce limited product range. In other cases, it turns out to be too laborious, because the actual cost of the commodity party becomes known only at the end of the reporting month, and the sale of products is also during it. Therefore, the conditional assessment of products is usually used based on their vacation price (not including VAT) or planned cost.
- It is possible to calculate on the basis of the selling price, but only if it does not change during the reporting month. In other situations, accounting is carried out by planned cost The finished products that the planning department calculates on the basis of the actual over the previous month adjusted in accordance with the forecast of price dynamics (the accounting price is obtained).
- The goods produced are written off from the account of account 23 to the debit of account 26, and the cost of products already shipped by the buyer - from a loan 26 to debit 901. After at the end of the month the actual production cost will be calculated, calculate the difference between it and the accounting price, and Also deviations concerning the sale of goods.
When calculating cash costs, various factors should be taken into account, based primarily at the cost of the cost of the enterprise for the production of products), since it is directly dependent on the amount of profit and measures to be taken to increase profitability.
Essence and types of cost. Cost classification
The cost of production is the cost of the enterprise on its production and implementation, expressed in monetary form. Calculation and analysis of the cost of products is the most important task of any enterprise and enters the management accounting system, because It is the cost that is based on most managerial solutions.
Distinguish the planned and actual cost. The planned cost of production includes only those costs that at a given level of technology and the organization of production are necessary for the enterprise. They are calculated based on the planned norms of the use of equipment, labor costs, consumption of materials.
The reporting cost is determined by the actual cost of manufacturing products.
According to the sequence of formation, the cost of the technological (operating), workshop, production and complete is distinguished. Technological cost is used for economic Evaluation Options for new techniques and choosing the most efficient. It includes costs that are directly related to performing operations over a specific product. The shop cost has a wider range of costs: in addition to technological costs, it includes the costs associated with the organization of the workshop and the management of them. Production cost includes production costs All workshops occupied by the manufacture of products and the costs of general management enterprise. Complete cost includes production costs and exproductive (commercial) costs.
The selection of such types of costs as individual and medium-wide allows you to create a base for determining selling prices (wholesale). A combination of the costs of a separate enterprise on the production and sales of products is an individual cost. The average consumer cost is characterized by the production costs of this product on average in the industry.
Economic essence, the costs of production and sales are divided into expenses on economic elements and calculation articles.
Allocate the following economic elements:
- material costs (minus return waste);
- labor costs;
- social deductions;
- depreciation of fixed assets;
- other costs.
Material costs include:
- the cost of raw materials acquired and materials;
- the cost of purchased materials;
- the cost of purchased components and semi-finished products;
- the cost of works and services of a production nature paid by third-party organizations;
- the cost of natural raw materials;
- the cost of all types of fuel consumed on the fuel consumed on technological purposes, the production of all types of energy, the heating of buildings, transport work;
- the cost of purchased energy of all kinds spent on technological, energy, motor and other needs.
From the cost of material resources included in the cost of production, the cost of waste implemented is eliminated.
Under the departments of production are understood as the residues of raw materials, materials, semi-finished products, coolants and other types of material resources, formed in the process of production, which have lost their entirety or partially consumer qualities of the source resource. They are implemented at a reduced or cost price. material resource, depending on their use.
The cost of paying for labor includes the cost of labor of the main production personnel, including premiums that stimulate and compensate payments. Social deductions include compulsory social insurance deductions, to the Employment Fund, pension Fund, on the health insurance.
Depreciation of fixed assets is the amount depreciation deductions On the complete restoration of the main production assets.
Other costs - taxes, fees, deductions extrabudgetary funds, payments on loans within rates, business costs, training and retraining of personnel, rental fees, depreciation intangible assets, repair fund, payments for compulsory property insurance, etc.
By classification of costs for economic elements, it is impossible to determine the costs directly related to the production of a particular product, therefore, the costs of calculating items are carried out.
Allocate the following cultural articles:
- Raw materials and materials, minus realized waste.
- Purchased semi-finished products and components.
- Fuel and energy on technological purposes.
- The main salary of production workers.
- Additional wages of production workers.
- Executions for social needs.
- Tool wear and devices target And other special costs.
- The cost of maintenance and operation of technological equipment.
________________________
Total technological cost - Workshop costs.
________________________
Total workshop cost - Hostess-based production costs. TOTAL PRODUCTION COST
- Exproductive costs.
________________________
Total total cost
In the formation of actual costs, the costs of warranty repair and warranty service of products are taken into account that the warranty service life is installed, losses from downtime for inspection reasons, shortage material values in production and in warehouses in the absence of guilty people, benefits due to disability due to production injuries paid on the basis of court decisions, payment of employees released from enterprises and from organizations in connection with their reorganization, reducing the number of employees and staff, and Also losses from marriage.
Classification of costs for calculation articles underlies other expenses classifications included in the cost of production.
The following classification features are distinguished when the cost division:
- attitude to the production process;
- attribution to the cost;
- dependence on production volume.
In relation to the production process, expenses can be the main and overhead; At the cost of the cost - direct and indirect. Depending on the production volume, costs may be conditionally variables (proportional) and conditionally permanent (non-reparitional).
Calculation cost of products
Calculation of cost is one of the main tasks of management accounting in the enterprise. In cost estimates, the material costs of fuel and energy, purchased semi-finished products and components are direct costs and are included according to current costs of consumption and prices for the product.
The main salary of production workers includes wages on a product designed for labor intensiveness or time-spent rates and tariff rates. Additional salary takes into account payment for unreought-after time.
Social deductions include social insurance, Pension Fund, Employment Fund, Mandatory Medical Insurance and is carried out in accordance with applicable law.
Wear tool and targeted tools and other special costs are included in the cost of production monthly depending on the regulatory life of the tool and snap.
The costs of the content and operation of the equipment are comprehensive costs, they include:
- costs of maintenance of equipment and remuneration of workers workers engaged in service maintenance, mandatory deductions, repair and depreciation costs;
- reimbursement of wear of low-value and high-speed tools and costs for their recovery;
- other expenses.
The costs of the content and operation of equipment (RSEA) can be included in the cost in proportion to the main wage of the main production workers (OZPR) or the method of estimated (regulatory) rates calculated on the basis of the coefficient-machine-hours. The estimated bet is the value of the cost of maintenance and operation of equipment for the hour of the equipment on which the product is manufactured.
The calculation is performed in the following order. For each workshop, the technological equipment is combined into homogeneous groups. It establishes the value of operating costs per hour of equipment. For each product (parts, node), the time spent on processing (operations) this kind technological equipment. In accordance with this time, the costs of the content and operation of technological equipment on this product are included in the calculation.
Cost expenses include:
- fund of remuneration of workshop staff with deductions;
- maintenance of buildings, facilities and equipment of workshop, including property insurance, repair and depreciation;
- costs of rationalization and inventive work;
- labor protection costs;
- reimbursement of wear of a low-value and high-speed inventory; other expenses.
The workshop costs in the cost of the unit of products are included in proportion to the sum of the main salary of the main production workers and costs for the maintenance and operation of equipment.
The general production costs include:
- costs related to production management, including the Fund for remuneration of management personnel with deductions, business costs, maintenance and maintenance of technical means and management (MC, communication nodes, alarm means), payment of consulting, information and audit services, bank services, representative expenses;
- costs for training and retraining of personnel;
- tests for testing, experiments, research, the maintenance of public laboratories;
- labor protection costs;
- costs for the content of fire, militarized and watchdogs;
- general expenses - Insurance, maintenance, maintenance and depreciation of fixed assessment funds;
- taxes, fees and other mandatory deductions.
In general production costs are the cost of paying interest on bank credit Within the rate established by law, as well as depreciation on intangible assets, including patents, licenses, "know-how", software products.
Commercial (exproductive) costs include costs for packaging and packaging, the cost of delivering products to the station station, as well as the content of personnel providing normal operation from the consumer within the established period.
Commercial non-production costs are calculated as a percentage of industrial costs (3-7%).
Calculation methods
Calculation methods - Calculation method depending on the calculation unit. There are 2 groups of cost calculation methods: preliminary calculation methods and production calculation methods.
The first group of methods includes:
- specific cost method;
- aggregate method;
- ballest method;
- parametric method.
Second group of methods:
- forgative;
- marked;
- normative.
Swelling method. For a significant amount of machine-building products, there is a dependence (linear, power) between one of the parameters of the machines and the cost of their manufacture.
where SYI is the specific cost of the existing design per unit parameter, rub.; Ni - the value of the defining parameter of the new design.
In engineering, the specific costs per unit mass of construction (metal-cutting machines, steam turbines are most developed; In the electrical industry - from technical parameters (power of electrical machines, etc.).
Aggregate method. It is based on the cost of the cost of the production of individual structural parts and aggregates, the value of which is known. On a similar principle, a unified system of automation means is created - GSP.
The ball method is estimated by the scores of each technical and economic indicator of the product, which is associated with certain consumer properties of the new design. Such an assessment is performed on special estimated scales in which the number of points depends on the level of a particular product quality indicator.
The parametric method allows you to find the cost of the relationship between the value of the complex of technical parameters of similar products and the cost of their production. Such dependences allow to construct correlation models that establish corresponding links in mathematical form.
The accounting method of calculation is used mainly in individual and small-scale production at mechanical engineering enterprises, instrument making, manufacturing non-refining specimens or small batch of products. The essence of the scoundal method is that production costs are accounted for on separate orders. The actual cost of the order is determined at the end of the manufacture of products or works belonging to this order by summing up all costs. For calculating the cost of the product unit, the total amount of the cost commission is divided by the number of products issued. The method has a drawback: Order fulfillment usually does not coincide in time with the calendar periods taken in plan, and this causes significant fluctuations in the cost of the same names issued in different months.
The seed calculation method is used at metallurgical, chemical, petroleum, textile, paper, and other industries (in production with repetitive homogeneous material and product processing technology). Redone - part of the technological process. Cost is determined by separate redo technological process. Streamly calculation is especially necessary in cases where the products of individual conversion (semi-finished products) are supplied to other enterprises. The normative method of calculation is used mainly in enterprises with mass and serial production in mechanical engineering and instrument making.
Regulatory calculations are based on reasonable expenditure rate on all calculation articles, the actual cost is determined on the basis of deviations from the normative. The method is used in all sectors of production for both calculation purposes and to carry out current cost control.
Product price. Profit
The price is a monetary expression of the cost of a unit of goods. The price performs 4 basic functions:
- accounting;
- distribution;
- stimulating;
- regulating.
The price account function is implemented in the mercy of the goods, distribution - in the distribution national incomeStimulating - in stimulating scientific and technological progress and production development, regulating - in regulating supply and demand. In practice, there are several price classifications:
- on the maintenance of turnover;
- on the territory of action;
- by time;
- according to the degree of freedom from the impact of the state in their definition;
- on the distribution of transportation costs.
For the maintenance of turnover, the wholesale prices of enterprises, vacation prices of enterprises-manufacturers, retail prices, purchase prices, tariffs are distinguished. Wholesale price of the enterprise includes full cost and profits.
The selling price is formed on the basis of the wholesale price with VAT (value added tax) and excise tax (for excisable goods).
Retail price is a vacation price taking into account trade premises (extra charges), which include the costs of trade organizations, profits and value added tax of trade services. Scheme 1 shows the formation of a retail price.
Complete cost
+
_______Profit_______
Wholesale price of the company
+
VAT
+
______ [excise] ______
Vacation price of the company
+
___________ trading allowance __________
Retail price
Purchasing prices are prices (wholesale), according to which agricultural products are regulated by collective farms, state farms, farmers and the population. Prices are negotiable, the difference between their vacation and retail is that they include VAT and excise taxes in their composition, because they are not included in the price of purchased agriculture material and technical resources. Tariffs are divided into tariffs of cargo and passenger transport and paid services to the population.
The classification of prices on the territory of the action highlights the prices of uniform (waist) and regional (zonal). Single prices are established and regulated by federal bodies (gas, electricity). Regional prices are regulated local bodies Self-government (utilities, purchase prices, tariffs for paid services to the population.
The classification of price prices is divided into permanent (relative to a certain period of time), temporary, seasonal, stepped, "for a term". Currently, there are no permanent prices in the domestic economy, because The greatest period of their action is determined by the level of inflation. Temporary prices are established for the period of development of new products, seasonal prices are used in industries, processing agricultural products. Step prices are associated with stages life cycle The goods achieve extremely high values \u200b\u200bduring the growth and sharp rise in demand for the new, "pioneer" product. Prices "For a term" currently act as contract prices, in the presence of a contract for the implementation of any products. The conclusion of the contract for the next term implies their change. A variety of contract prices are negotiable prices.
The degree of freedom of prices from the impact of the state, when determining, allocates free prices, price regulation and fixed prices. Free prices add up in the market under the influence of supply and suggestions, adjustable prices are also formed as a result of the oscillations of the market situation, but the state exercises either their direct limitation or regulation of profitability. Fixed prices are established by federal management bodies on a limited circle of goods.
Classification of prices for distribution of transportation costs is called a fan system ("Franco" - free from payment). The essence of the system is that the cost of transportation of products to the destination specified in the "Franco" carries the supplier of products, and the rest is the buyer.
The cost of trade is made up from the cost of the supplier, as well as cash flow on logistics (delivery). This indicator is used in the calculation of margin and profit in management accounting, in tax reporting and affects the amount of taxes. It is at cost that it is written off from the warehouse sold goods, and on how it will be calculated dependent financial reports and indicators. The complexity of calculating the cost in trade is related to the fact that the goods usually bring parties, and they sell the piece. In this case, it is almost impossible to understand the accurate cost of each sold position. Therefore, there are several allowed cost estimation by law. Consider in more detail those methods that are most commonly used in retail.
According to the cost of goods
Calculation at the cost of each unit, a rather rare case in trade. Used to take into account unique, piece goods, differing in price. For example, in jewelry stores. You can use this method, if you always know, from what shipment the goods sold was. Those. If you have the opportunity to calculate the exact cost of each position, which is in stock.Middle Cost
When the goods are brought by parties, it is difficult to determine which delivery was one or another item sold. But for the method of average cost this is not important. It involves the calculation of the cost of the average arithmetic times a month.The method is suitable for companies leading to notebooks, without special automation tools.
The calculation of the average cost of goods can be expressed by formulas:
middle Cost \u003d (the cost of residues at the beginning of the month + the cost of the goods received for the month) / (the number of goods at the beginning of the month + the number of goods received for the month)
the cost of the written off product \u003d (average cost) x (number of goods sold per month)
Suppose you in the warehouse have 100 positions of one unit of goods for 20 rubles. During the month, 2 more buses of the same product came: 50 pieces of 18 rubles and 50 pieces of 16 rubles. You sold 160 positions for 25 rubles (4000 rubles). Calculate profits.
Middle Cost:
(20x100 + 18x50 + 16x50) / (100 + 50 + 50) \u003d 18.5 (rub.)
The cost of the debited product:
160x18,5 \u003d 2960 (rub.)
Profit:
4000 – 2960 = 1040 (rub)
A fairly simple calculation method, but not always favorable from the point of view tax accounting. For example, when the cost of the goods you buy is gradually decreasing (which often happens when purchases from a permanent supplier).
Most optimal method is the maintenance of partion automated accounting and the calculation of the cost of the FIFO method.
FIFO method (FIFO)

Consider the same example. In stock 100 positions for 20 rubles, and for the month there were 2 supplies: 50 pieces of 18 rubles and 50 pieces of 16 rubles. Sold: 160 positions for 25 rubles.
First of all, 100 positions are written off on 20 rubles (2000 rubles), then 50 to 18 rubles (900 rubles) and another 10 to 16 rubles (160 rubles).
Profit:
160x25 - (2000 + 900 + 160) \u003d 940 rub.
The profit indicator in this case is lower than when calculating the average cost. Those. Profit tax will be less.
Most often, it is precisely such a method for estimating the cost when debiting goods from a warehouse is most profitable for the entrepreneur.
Organization or IP independently chooses a cost estimation method and, according to 313 article tax Code RF, informs about it tax authorities once a year.
If you use, the write-off of the products on FIFO, as well as piece goods (at the cost of each unit) is automatically produced.
Only by estimating these two indicators, it is worth deciding on the start of new activities.
The costs of the greatest proportion, as a rule, is the cost of production (works, services). To calculate it, we need certain skills and knowledge.
However, the problem of calculating the cost is no less relevant and for the current business, since in order to reduce costs, it is necessary to clearly understand what they are developing and for which values \u200b\u200bcan affect, and which are not.
Determine the composition of the costs that will form the cost
At various enterprises, the composition and structure of costs are different and depend on many factors. However, there are types of expenses, relevant to all. They can be combined into several groups or articles (look at the table). At the same time you have the right to decide which of these expenses will form your cost. Depending on the range of expenses that you consider, there are three types of costs:
- complete cost (or cost of sales);
- full production cost;
- incomplete production (shop) cost.
Typical category grouping to calculate cost
N p / n | Article costs | Type of cost | ||
Incomplete production | Full production | Full | ||
1 | Raw materials and materials | + | + | + |
2 | + | + | + | |
3 | + | + | + | |
4 | + | + | + | |
5 | + | + | + | |
6 | + | + | + | |
7 | Commonwealth | + | + | + |
8 | General production expenses | - | + | + |
9 | Losses from marriage | - | + | + |
10 | General running costs | - | + | + |
11 | Commercial expenses | - | - | + |
The "+" sign indicates the costs of the costs that are taken into account when calculating the cost of a particular type; Sign "-" - those cost articles that are not taken into account.
Please note: the above types of cost are not mandatory for calculation. You yourself decide what costs you include in the calculation, which is not. This is a question of your internal management accounting. On the calculation of taxes, the method of calculating the cost is not affected by you. Because all taxes are considered by the rules of tax accounting. And the calculation of the cost is an element of management accounting, as it takes place in the interests of the owners and business executives. At the same time, in accounting, the cost is reflected, so the list of costs forming its costs accounting policies for purposes accounting.
We distribute indirect expenses
The costs that can be included in the cost is not the same in nature. There are those that can be directly attributed to the cost of a particular product. For example, you sew dresses and trousers. And the buttons are used only in the sewing of dresses, and the buttons in the trouser sewing. That is, you know exactly how much the material is where it goes. Accordingly, the cost of buttons will form the cost of dresses. And the cost of the buttons is the cost of trousers.
Such expenses are called straight. And to them, as a rule, include three studies:
- on raw materials and materials;
- semi-finished products, components;
- fuel and energy for production goals.
Most costs cannot be so easily attributed to a specific type of products, since they are associated with the production of all products or with the activities of the entire company as a whole. Therefore, such expenses (they are called indirect) are distributed. The distribution method is also indicated in the organization's accounting policy. You can choose one of the following distribution databases:
- production time of production workers;
- salary of production workers;
- direct costs;
- the cost of basic materials;
- the number of products manufactured.
The procedure for the distribution of indirect costs between types of products you are installing yourself. The selected way to secure in accounting policies.
Example 1. Distribution of indirect expenses
LLC "Light" produces three types of bakery products: French baguettes, rye pellets and wholebreaker bread. The cost of each type of product produced includes common expenditures. Their amount for the month amounted to 12,500 rubles. The base for the distribution of general expenses is chosen the amount of direct costs for the production of individual types of products (main raw materials). These costs in the reporting month are equal to 85,000, 64,500 and 120,000 rubles. respectively. Total costs for the acquisition of fixed raw materials - 269 500 rubles. (85 000 rub. + 64 500 rub. + 120 000 rub.).
The accountant calculated the distribution coefficients of indirect costs. They amounted to:
- for French baguette - 0.32 (85,000 rubles: 269 500 rubles);
- rye pellets - 0.24 (64 500 rubles: 269 500 rub.);
- whole grain bread - 0.44 (120,000 rubles: 269 500 rub.).
Taking into account the coefficients obtained, generality expenses by types of products were distributed. The total amount was:
- for French baguette - 4000 rubles. (12 500 rubles. X 0.32);
- rye pellets - 3000 rubles. (12 500 rubles. X 0.24);
- whole grain bread - 5500 rubles. (12 500 rub. X 0.44).
Dunnesses for calculating cost
The actual cost is calculated on the basis of specific costs. And for this use accounting data. You will need to collect information on all costs of the costs that form your cost price.
If we are talking about materials, then their movement is reflected in the reports of financially responsible persons or card accounting cards. And directly consumption of raw materials are drawn up with the help of overhead requirements for materials leave. Accrued wages Conduct in estimated statement. All other expenses should also be decorated acquittal documents. Least accounting certificatein which it is important not to forget to specify all mandatory details "Pervichki".
Full information from the Company's primary accounting documents reflect on accounting accounts. Then the corresponding amounts accountant writes off, forming the cost. The rules for which it should be done are shown in the table.
How to write off in accounting costs for production
Procedure for accounting costs | Write-off on the results of the reporting month | |
If costs form the cost | If costs do not form the cost | |
Direct expenses | ||
Reflected on the debit of account 20 "Basic Production" on analysts by product types | Speakers on account 43 "Finished products" costs that are coming on finished products. From account 43, in turn, write on account 90, subaccount "cost of sales", the costs that fall on the products implemented. At the same time on accounts 43 and 90, lead analytical accounting by types of products | - |
General and general production spending | ||
Reflected on the debit of account 25 "general production costs" | Spread amounts on account 90. At the same time, the subaccount "Sales cost" do not use, start a separate subaccount "general production costs" | |
General running costs | ||
Reflected on the debit of account 26 "General expenses" | Spariate the costs of 20 on the appropriate analysts by product types | Spariate the amounts on account 90. At the same time, the subaccount "Sales cost" do not use, start a separate subaccount "Management expenses" or "general expenses" |
Commercial expenses | ||
Reflected on the debit of account 44 "Sale expenses" | Spariate the cost of 90, subaccount "Cost of sales", on the appropriate analysts by product types | Spariate sums on account 90. At the same time, the subaccount "Cost of sales" Do not use, start a separate subaccount "Commercial expenses" or "Sale expenses" |
What way to determine the cost of the unit of products? It is not always possible to determine how much the materials goes to the manufacture of one unit of products. In this case, it is allowed to consider the cost per group of products. For example, 100 pieces or 1000 pieces - depending on what you produce.
If the costs of the product costs are not to be specified, nothing remains, how to consider the cost of all manufactured products in general. This is the so-called boiler metering method. After you calculate such a common cost of "on everything", determine the average cost of the unit of products.
The calculation algorithm is next. Divide the total cost on the volume of manufactured products. For example, the cost of 100 units of products amounted to 82,350 rubles. It means that the cost of one unit is equal to 823.5 rubles. (82 350 rubles: 100). And then the cost of a unit multiply by the amount of products implemented and thereby get the cost of sales.
Calculation of the cost of a unit of product is necessary because it is necessary to know not only the "price of production", but also to own information on the value of values \u200b\u200bshipped to the warehouse, implemented, etc.
If there is no actual data, and you wish to predict the future cost, take the planned data. By material costs Excel from the need for raw materials on the product. By salary, follow the official salary of your workers. Other expenses are planning on the basis of your needs, focusing on the contracts enclosed by you or the average market prices. To do this, spend your own market analysis.
Registration of the calculation of the cost
The form of a document in which the cost will be calculated, you develop yourself and consolidate in accounting policies. In the same calculation or separately, if necessary, you can decipher the specific indicators.
Example 2. Calculation of production costs
LLC "Mir" produces stools and stands. In each case, according to the accounting policy of the enterprise, an incomplete production cost is considered.
At the beginning of January 2014, the balance of finished products in the warehouse was absent. During the month, 100 units of stools and Tumbers were started and completed. At the same time, 50 stools and 45 Tumbers are implemented in January. Cost articles and their value expression Accountant led in the calculation.
Calculation of the actual cost of 100 units of production, completed production in January 2014, rub.
N p / n | Article costs | Stools | Tombs |
1 | Raw materials and materials, including: | 34 550 | 77 100 |
Wood | 23 000 | 52 000 | |
Metal | 2200 | 4000 | |
Plastic | 550 | 380 | |
Nails | 1800 | 2720 | |
Paints | 7000 | 18 000 | |
2 | Semi-finished products, components | - | - |
3 | Fuel and Energy for Production Goals | 11 835 | 16 880 |
4 | Salary of production workers | 48 000 | 96 000 |
5 | Insurance fees with wages of production workers | 15 360 | 30 720 |
6 | The cost of maintenance and operation of equipment | 2200 | 1000 |
7 | Commonwealth | - | - |
TOTAL | 111 945 | 221 700 |
In total, the cost of one unit amounted to:
- on stools - 1119,45 rub. (111 945 rubles: 100);
- on the couches - 2217 rubles. (221 700 rub .: 100).
Total sales cost for January amounted to:
- on stools - 55 972.5 rubles. (1119,45 rub. X 50);
- on the couches - 99 765 rubles. (2217 rub. X 45).
Nuances requiring special attention
The procedure for the formation of the cost of production will write out in detail in accounting policies for accounting purposes. After all, the cost is not only managerial, but also an accounting indicator.
If the cost is not included in the cost of general and commercial expenses, in the account 90, in addition to the subaccount of "Cost of sales", pride separate subaccounts "Management Costs" and "Sale Expenditures".