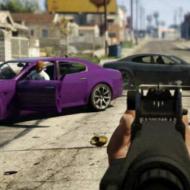
Warm climbing. Well laying - laying and application features. Welding brickwork
One of the ways of insulation during the construction of the house is the wellwork for walls of bricks. The technique consists in the construction of the inner and outer part of the structure, between which the well is left to fill with thermal insulation materials. This method saves on the insulation of the room and reduce the pressure on the foundation of the construction.
Characteristic
Benefits
Before starting construction work, it is necessary to correctly select building materials in order to avoid disorders of the insulation of the room.
Well laying is built in such a way that the opening between the two parts of the wall in the Polkirpich is filled with thermal insulation material. Brick structures are connected by reinforcement pins with curved ends. The use of masonry with insulation has such advantages:
- saving bricks up to 18% compared with ordinary masonry;
- weight loss and design volume;
- lack of condensate in the cavity of the well;
- the ability to apply on the front of the wall of economical material, such as silicate or ceramic brick;
- refractory;
- aesthetics of the species.
disadvantages

Well brickwork has many advantages, but if you do not consider some nuances, you can get such unwanted effects:
- Reducing the homogeneity and strength of the structure. To prevent this disadvantage, it is necessary to calculate, where and in what quantity is the horizontal and vertical diaphragms, which will ensure the enhancement of the structure.
- The formation of condensate inside the well in the winter. To avoid such an effect, the inner side of the well must be chosen by a vaporizolation layer. At the same time, ventilation gaps are made of at least 10 cm. In the region of the upper and lower row, vertical seams are cleaned, which ensures the convection convection.
- The destruction of the insulation when exposed to high temperatures in the summer. The use of special heat-resistant insulation materials will prevent the insulation disruption.
Where is used?
There is a wide use of well masonry in the construction of such structures:
- outer walls of a residential building;
- multi-storey buildings;
- used buildings.

This method should be confused this method of laying the wall with construction, when the sewer of the brick or well is made. At the same time, the pit laying is made from the inside with a solid closure of bricks to the top. A plumbing hatch is done to pump out of excess water. In addition, when the well construction is left, the hole is left to remove the tap pipes. Alternative to brick masonry are concrete rings well.
Consumption of materials
Cleaning masonry made of bricks can significantly reduce the amount of bricks in comparison with a solid design. The calculation of the necessary funds is carried out by a mason who will perform work. For construction, such materials will be needed:
- Brick. Most often used ceramic, as it is moisture-resistant. The calculation of the required amount is made on the basis of the cost of consumption of building materials.
- Solution. It consists of sand, cement and water or a special adhesive mixture.
- Failure. As a heater, such bulk products such as slag, clayzit, sawdust can be used.
- Terkesolation materials. Special building materials, such as glass gamble, mineral wool and expanded polystyrene provide reliable thermal insulation of the room.
- Funds for reinforcement. Reinforcement grids, steel wire or fittings bent around the edges can be used.
How to do?
Lightweight type design

The laying of wells at this type of work is carried out by two rows, between which the cavity is formed in the form of a well. After 2-5 rows, the design is fixed by the tiley nearby. If the length of the wall is more than 1.5 m, it is reinforced with steel wire. A feature of such a design is that voids are filled with a solution of concrete to the very top. This type of wall is most often used for non-residential premises that do not need heat retention. The filling of the wells is carried out in stages based on the sinking rate of the solution.
Fig. 1 Well laying
A - masonry fragment; B - ordinal layout of bricks when laying a straight angle of the wall; 1 - insulation; 2 - Aperture of tile bricks
This construction technique reduces brick consumption by 15-20% compared to solid brickwork. Variants of well-masonry are characterized by different capital capacity and stability (Fig. 2).
Fig. 2 Versions of Well Masonry - Top view (in mm)
A - Well laying in two bricks; B - Welding masonry 2.5 brick: in - modified well laying; 1 - brickwork; 2 - thermal insulation; 3 - foam concrete
The layers in the well masonry are connected by vertical diaphragms, the distance between which should not exceed 1170 mm. In fig. 3 is given a laying plan with an inception of the inner wall.
Fig. 3 Lightweight Wellwork with Inside the Interior Wall (sizes in mm)
A - a masonry corner plan; B - a masonry plan for adjusting the inner wall to the outer; 1 - transverse vertical diaphragm; 2 - Beep insulation
It goes without saying that the strength of the wall in the wellwork is reduced. Therefore, at the lower level of the slabs of the overlap and two rows below the window openings throughout the perimeter of the outer and bearing walls, horizontal dissolved diaphragms are arranged.
Fig. 4 Lightweight masonry with mortar diaphragms
A - with brick diaphragms; B, b - with mortar diaphragms reinforced steel reinforcement; 1 - Flooding or lightweight concrete; 2 - reinforcement steel; 3 - Solution
Such diaphragms are formed by the reinforcement grid, which is raised simultaneously to the internal and outer layers of masonry and protect the layer of sandy-cement mortar. The disadvantage of well-masonry is increased air infiltration through air cavities.
Fig. 5 Corner Lightweight Well Masonry (sizes in mm)
1 - transverse vertical diaphragm; 2 - Beep insulation
Longitudinal walls of the wells are laying out with spoonful rows. The second row of the outer and inner miles is laying out with spoons, the transverse walls of the wells - tile. Dressing transverse walls with longitudinal are carried out through a row.
Wells begin to fall asleep after the construction of 4-5 rows of masonry. Corners with three-row diaphragms significantly increase the strength of the structure.
Fig. 6 Angle laying with three-row diaphragms
1 - insulation; 2 - Missile screed; 3 - plot of solid masonry; 4 - mortar screed; 5 - diaphragms of three rows of masonry
A feature of these walls is a solid laying in the corners. The construction of the angle is starting with the laying of two three-taps in the outdoor verst. From the first to the third, the third row leads a solid laying with a single-row dressing system.
In the level of the fourth row, leave the place to lay the insulation. On top of the insulation make a dissolve screed, in which the angle of the angle continues in the same sequence.
In the construction of plumbing and sewage networks, the construction of wells is the most responsible task. These are not only drinking, but also drenched, viewing and swivel wells, various septic tanks and sumps.
For their facilities, various materials are used: stone, wood, metal pipes, concrete, plastic. Laying a wodge of a brick, at the same time, deserves special attention for the simple reason that it is easy to perform with their own hands.
Moreover, if you use a brick for this purpose, the price of the well will pleasantly surprise you.
Device of a brick well
Most often, the laying of the brain of brick is used in the construction of network tanks. Depending on the purpose, they can have both round and rectangular or square shape.
So:
- Laying of wells, the depth of which does not exceed six meters, is usually located below. There is another way of building walls, called squeaver - it is used in deeper mines.
Most often, it is drinking. - We will tell about the construction of the laying from the bottom-up, and the video in this article will help you better assimilate information. So, if we are talking, for example, about an observation or swivel well, the masonry of its walls should be made on a concrete base.
- It can be performed both in a monolithic method and arranged with the use of reinforced concrete slabs. The size of the bottom should slightly exceed the area of \u200b\u200bthe well, taking into account the thickness of its walls.
- To start the masonry and give the right shape of the well, markup is applied to the base.
First, it is necessary to draw perpendicular axes: transverse and longitudinal. The point of their intersection will be the center of the well. - If its mine has a square shape, you need to delay the internal perimeter. For a round configuration well, an internal circle of walls are placed on the base.
- Walls of any structures that are erected from brick require additional gain, and the wells are no exception. Only strengthening methods in each case are used different.
Anticiping your question: "What are the well put on the bottom before laying out the first row?", I immediately say that in the case of round wells, it is a wooden or metal frame. - In general, throughout the height of the brickwork, three frames of the corresponding diameter are installed. The lower, or the main frame is the largest, it exceeds the diameter of the intermediate and upper frames by 50 mm.
By the way, this frame can be performed from reinforced concrete. The thickness of the lower frame should be at least 10 cm. A steel knife is installed on the outer side of this frame. - To increase the strength of the masonry, the frames are connected between themselves with metal rods with a diameter of 12-15 mm. In the size of their cross section in the frame drilled holes.
Six rods insert into the lower frame. From above set the frame intermediate. For it, for connecting to the upper frame, the reinforcement is also mounted, but not six, but twelve rods.
- A thread must be cut on the reinforcement, since its mounting to the frames will be carried out using nuts. The resulting frame will ensure the rigidity of the entire design, and will not allow the walls of the well to collapse, even if the natural movement of the soil occurs.
- When building a well, the lower frame with a knife will allow you to lower the well segments without any problems. Only in this case the frames may not be three, but much more - it all depends on the depth of the structure.
- The main task you need to decide before the start of the walls of the walls is the absence. If the moisture seeps into the mine, it is pumped out.
Naturally, during the rain, such work is also not underway - the water is flushed out of the seams not yet a climbed solution. - For those who have never been involved in masonry work, the easiest way to make a template, simulating the section of the well walls. After installing the frame, the brick is folded along the outer edges.
The photo below is clearly visible how to do it. The walls of the round well lay out in such a way that the chock row of bricks formed its inner circle.
- Then you can start kneading the solution. The component composition of the solution is a mixture of one part of the cement and three parts of the sifted sand.
Water in solution should be so much to get a thick, elastic solution. - Under the first row, it is imposed directly on the frame. If it is concrete or wooden, it is better to be pre-laying the rubberoid strips.
- Vertical seams that differ significantly from the outside of the masonry are carefully filled with a solution. When erecting a well-diameter well, the expansion of the jacks between bricks can be quite significant.
- In order to save a solution, as well as to increase the strength of the seams, brick fragments are laid, large crushed stone, or clay. To make it it was convenient, between the walls of the mine and the well there should be a clearance of at least 20 cm.
Then his layers fall asleep with a sandy-gravel mixture, and in the upper part - clay, which is thoroughly trambed. - Depending on the depth of the well, the thickness of its walls can correspond to one length of the brick (25 cm), or to be laired in a half of the brick (37.5 cm). The neck of the well having a round shape should be a little already than the diameter of its working chamber.
- For this, the masonry is gradually narrowed, but only from three sides. From the sheer side, protrishes are usually built, or installed metal brackets, allowing you to descend into the well.
The verticality of the wall must be controlled using a plumb. Bringing adjacent rows is performed due to a small displacement (in a quarter of the brick). - Two lower rows will be tiley, and then, they can alternate with spoonful, every three or four rows. Alternating rows will serve as a guideline for additional reinforcement.
In each fourth row, it is necessary to lay a steel wire or a thin strip. - To enter the pipes in the well, you need to leave holes in the course of the masonry. Where the rods of the frame will interfere with putting a brick, it will have to make cutting.
A little not reaching the level of the intermediate frame, the masonry stop. First you need to install the frame. - An intermediate frame is put on the free ends of the rods, and then rigidly fixed with washers and nuts. After installing it, as well as check the horizontal and verticality of the whole design, masonry work can be continued.
The junctions between the masonry and the frame should be carefully embedded with a solution.
As the height of the masonry increases, for the one who produces it, inside the well, it is necessary to establish the scaffolding. After performing several rows, the laying is desirable to immediately fly to cement mortar.
The plaster layer will increase the service life of the well, and protect it from the penetration of groundwater or the rigor.
Well laying for walls at home
In the low-rise construction of residential buildings is often a wellwork for walls of brick walls. This type of masonry deserves close attention.
First, it allows the most effectively to insulate the walls. And secondly, during the construction process, they can not only be insulated, but also to decorate. So, well laying: for and against.
So:
- Little details on the positive sides of this construction of the walls. For each region there are certain norms of the recommended wall thickness, which can be very significant.
- In order to save, taking into account the ever-increasing cost of energy resources, the walls, in theory, you need to do thicker. And this is economically irrational: the cost of buying bricks will increase, and the foundation will need more powerful.
- For those who build a small private house, such difficulties have nothing difficulties. Get more warm brick walls with the smallest financial costs will help well laying with clay.
- Of course, it is possible to use and rolled insulation, but then the cost of construction will increase. Perhaps, perhaps only polystyrene crumb and expanded vermiculite can become a good alternative to the ceramzit.
Granular insulation falls asleep in the "Well" of the wall formed in the process of its construction. - Such a design significantly reduces the load on the foundation on the weight of the walls. And if for the construction of the hollow brick, the outer walls will be easier for another quarter.
Laying brick well has only one minus: it is not monolithic, as it has emptiness. For this reason, the building that has similar walls decreases the indicators of capitalities and seismic resistance. - In fact, the wellwork is a three-layer design consisting of the main wall, insulation, and the front wall. Both walls in the process of masonry are toughly bind to each other.
To enhance the design, various techniques are used, for example: the main wall is erected from full-scale brick, and facial from the hollow.
- The inner space of the two first rows can be filled with not insulation, but by a solution, representing a monolithic belt. In horizontal seams, after 4-5 troughs, reinforcement with a steel mesh or strip is performed.
- Due to the performance of the horizontal and vertical dressing of the seams, and the wells are obtained, closed on all sides. If bulk materials are used as a heater, in order to avoid their shrinkage, every 50-60 cm, horizontal diaphragms made of bricks of bricks are performed.
Currently, at least four options for performing well-masonry are applied: lightweight (pollipich), one and a half bricks, in two bricks (sometimes two and a half), modified.
We will not describe the details of these methods. If necessary, you can easily find the necessary information on the Internet.
Laying stoves
Laying wells are kept similarly, the scheme of which is very similar to some ways of the well-masonry walls of the house. In oven construction, this type of masonry is used to reduce the thermal conductivity of the walls.
So:
- The well formed between the inner and outer wall, as well as in the case of outer walls, is filled with insulation. In addition to those materials that we mentioned in the previous chapter, various types of mineral wats can be used here. Wells can be filled and any light concrete.
We led you a scheme, with the help of which the laying of the stoves of the furnace can be performed with their own hands. By the way, this method is used not only for the masonry of the oven itself, but also for the construction of the chimney.
Brick is the most common material for the construction of bearing walls. It is successfully used both in multi-storey industrial construction and private low-rise buildings. The only lack of bricks is low thermal insulation qualities. To solve this problem, an additional warming of the walls is performed. Brickwork with insulation inside makes it possible to build a warm house with minimal time and finance costs.
Cons Masonry without insulation
More recently, the issue of thermal insulation of brick buildings was resolved in a simple way - an increase in the wall thickness. Thus, for the middle strip, the thickness of the walls was 3-3.5 bricks, and in the northern regions she could reach 1-1.5 m. This is due to the high thermal conductivity of the brick, which causes large heat loss.

Such thickness was a forced measure in the absence of efficient and inexpensive thermal insulation materials. Another factor contributing to the use of "thick walls" technology in Soviet times was the relative cheap brick. This allowed to simplify the laying technology at the expense of refusal to use thermal insulation materials.
However, recently, a similar approach becomes too wasteful with a financial point of view: in addition to the cost of a brick, the costs of arrangement of enhanced base grounds are increasing.
Another problem with which you can encounter, arranging brickwork without heat insulation - displacement of the dew point inside the premises.
In construction, the dew point is the point inside or outside the street walls of the building, where the cooled pairs contained in the air begins to condense. The transformation of steam in the dew occurs when a warm air with cold surfaces is coming.

The most preferred option is to find the dew point outside the building, in this case the condensing moisture will simply evaporate under the action of wind and the sun. It is much worse if the dew point is shifted inside the premises. The dampness formed on the inner surfaces of the walls, negatively affects the microclimate in the house, becoming a source of high humidity and the reason for the appearance of fungus and mold.
Non-warmed walls in winter frosts are cooled to all their thickness, as a result, the condensation of the steam occurs on their internal surfaces.
In areas where minor temperatures are installed during the cold season, brickwork technology with insulation is the only acceptable.
Three-layer masonry
One of the varieties of the warmed wall is a three-layer brickwork. It looks like this:
- Inner wall of brick, slag blocks, aerated concrete, etc. Performs carrying function for inter-storey floors and roofs of buildings.
- . The insulation is placed in the inner cavities-wells between the outer and the inner walls. Protects the inner wall from freezing during the cold season.
- Outdoor wall with brick facing. Performs decorative functions, giving the facade an additional aesthetics.

On the image:
№1 - Interior decoration.
№2 - Carrier building wall.
№3 - insulation between brick masonry.
№4 - Ventilation gap between the inner insulation and facing wall.
№5 - Outdoor wall with brick facing.
№6 - Internal reinforcement connecting the inner and outer wall.
Brick masonry with insulation inside, like other construction technologies, has its pros and cons. To its positive qualities include:
- Little masonry volume, which reduces the estimated cost at the expense of savings on the number of building material.
- Little weight buildings, which makes it possible to use more easy and inexpensive foundations.
- High thermal insulation indicators allowing to maintain heat in winter.
- Improved sound insulation. The heat insulating layer can significantly reduce the noise level, which is especially important if the building is located on a central street with an intense traffic.
- External walls lined with decorative brick do not need additional decorative decoration.
Among the minuses of multi-layered walls can be specified:
- Large consideration associated with insulation, compared with brickwork at 3 - 3.5 bricks.
- Three-layer walls do not allow periodic replacement of the insulation, while its service life is always shorter than the service life of brick walls.
Selection of insulation
A wide range of insulation can be used as a heat insulating material, which meet the SNiP recommendations.
First, the thermal conductivity indicator of the material should be such to ensure the protection of internal premises at maximum minus indicators characteristic of this region.
You can familiarize yourself with the heat insulating indicators of the insulation in instructions from the manufacturer on its package or in the tables of technical specifications SNiP. By comparing these indicators with winter temperature minima, you can calculate the necessary thickness of the insulation layer.
Secondly, the insulation must have sufficient vapor permeability. Otherwise, the moisture will accumulate inside it, which will lead to the loss of thermal insulation qualities.
And, thirdly, the inner insulation must be fire-resistant. Thanks to its noncornsity, it will not only support the burning, but will create a flame retardant layer inside the masonry.
Mineral wool

The numerous family of insulation, created on the basis of mineral fibers, has excellent heat-saving characteristics. They are made by whipping in a centrifuge molten minerals: glass, basalt, slag, etc. The low heat transfer level in this case is achieved due to the high porosity of the material - the air layers do not allow the cold to penetrate through the minorvatu.
Absolutely not a fuel, but very afraid of dampness. When wetting, he almost completely loses its heat-saving properties, so when it is laying it is necessary to take care of the device for efficient waterproofing.
Polystyrene foam
Foamed - another frequently used thermal insulation material in three-layer masonry.

It produces it by saturation by air of liquid polystyrene, which, after frozen, acquires the type of porous round granules. To fill the wells in the wall, it can be used in the form of sheets or as a bulk material. He is much less Minvati afraid of dampness, but unlike her grief, so the walls, insulated with expanded polystyrene, should be protected from open fire. Even if the fire does not hurt the brickwork, it will cause burnout and the melting of polystyrene foam inside it. To replace the insulation, it will have to produce labor-intensive and expensive work on dismantling the facing part of the wall.
Bulk insulation
In private construction, sometimes three-layer masonry is made with filling in domestic wells with various mineral fillers: slag, claying, etc. A similar technique is somewhat cheaper and easier than the laying of the Ministry of Plight or sheets of polystyrene foam, but its effectiveness is much lower. This is due to the lower indicators of slag and ceramisit.
The slag is very hygroscopic - it is inclined to absorb and retain moisture, which may cause an increase in its thermal conductivity and premature destruction of the adjacent brick layers.
Masonry of three-layer walls

Wall masonry with insulation is performed in several stages.
- Laying of the inner wall. It is made according to the same technologies as the masonry of the ordinary carrier wall of full-scale brick, or building blocks. Depending on the minimum winter temperatures, it may have a thickness of 1 or 1.5 bricks.
- Masonry of the outer wall with facing. It is performed in such a way that the clearance required for laying or backfilling the insulation remains between it and the inner wall. Between themselves 2 walls can be connected either with connections from anchor bolts and fittings, or brick dressing carried out through certain intervals.
- Need to protect the insulation from dampness, as it is impossible to completely prevent moisture receipt through the brick.
- Filling the wells with a flowing insulation is made by reaching the walls of 0.8 - 1 m. Sheet and rolled insulation is attached to the inner wall using dowels-mushrooms with a wide plastic hat, after which it is closed by external facing masonry.
For the construction of the waterproofing layer, it is not recommended to apply "deaf" materials, such as rubberoid. This will exclude the possibility of free gas exchange between the external environment and the indoor premises of the house. In the outer wall every 0.5 - 1 m, leaving ventilation products should be left - the vertical seams between the bricks are replenished with a solution.
Three-layer brickwork allows you to solve many problems arising from the operation of housing in the winter. The process of erection of such walls is shown in the video below..
Brick houses have been erected for several hundred years, and many do it with their own hands. It is the brick that is the most common building material and at present. Released both full and hollow types of bricks.
Photo - Brickwork
Previously, almost all of the houses had the thickness of the walls of about 1M, which was associated with the lack of insulation in those times. Just with brick masonry with insulation, the massive construction of warm buildings and structures began.
Heatel between the walls
The difficulty of thermal insulation, both from the inside and outside consists of condensate. Water negatively affects not only thermal protection, but also on the entire design of the construction.
The thickness of the insulated layer of the insulation depends on a number of factors, such as:
- location of construction;
- wall material;
- wall thickness;
- type of insulated insulation.
Modern construction is regulated by the provisions of SNiP 23-02-2003, in which the required number of insulation is exactly indicated.
Types of brick masonry
There are 2 types of brick masonry by the arrangement of the insulation:
- masonry with the inner layer;
- masonry with outdoor layer.
Inner insulation
TECHNOLOGY OF WORKING WORKING, as follows:
- the foundation covered with a layer of waterproofing is laid by 2 rows of bricks closely;
- form 2 brick walls at a distance of 13-14 cm each other;
- every 3 brick horizontally make transverse diaphragms;
- to combine two walls into one system, wire bundles are used;
- the distance between the diaphragm bricks is set about 2.5 cm;
- window and doorways laid closely;
- close the wells also masonry close;
- the last row of bricks performs the function of the support, the bases of the rafter and the beams of overlapping are placed on it;
- waterproofing using a roll material.
The resulting wells are usually filled with insulation or light concrete, clay, slag, etc. Fucking material is tamped every half meter of frustration. The use of some materials requires the installation of an anticoned diaphragm.
Well laying with insulation is essentially a three-layer design, that is, it is a layered laying using an effective insulation, in the case of filling the wells insulation.
The advantages are:
- small thickness and weight;
- fire resistance;
- good appearance;
- the possibility of mounting at any time of the year.
Minuses:
- high laboriousness of work;
- high volume of hidden work;
- the need for continuous monitoring of the state of the insulation;
- low heat engineering homogeneity due to inclusions of concrete;
- the presence of cold bridges;
- bad maintainability.
Instructions for internal warming using mineral wool:
- mineral wool plates are laid throughout the perimeter of the wall;
- special anchors are mounted in the brick wall;
- fasten the plates on these anchors;
- early the second wall, leaving the gap between the insulation and the wall;
- slip and align the seams.
Quite often, instead of the same mineral wool or polystyrene foam in the wellwork, air gaps are used. Wall insulation between brickwork in this case is not produced. It should be borne in mind that the width of the air layer should not exceed 5-7 cm. The efficiency of such a method is much worse than using an effective insulation.
Warming from the inside of the room
With the heat insulating layer is placed on the inside of the wall.
Inner insulation
The use of internal insulation is permissible only in rare cases:
- when there is no possibility to change the appearance of the facade of the building;
- when the wall is the unheated room or the elevator mine, where to carry out insulation is unreal;
- when such a type of insulation is laid in the project of the building initially and is designed correctly.
Attention! The main problem with internal insulation is manifested in the fact that the walls themselves do not become warmer, but begin to freeze even more. This is due to the fact that the dew point shifts on the inside of the wall.
What happens when internal insulation:
- in the cold season, wall structures fall into the "zone of negative temperatures";
- permanent temperature differences lead to the destruction of materials from which walls are made;
- the inside of the walls due to cooling accumulates moisture;
- favorable conditions are obtained for the formation of mold.
Important! For internal thermal insulation, fibrous insulation cannot be used, since they are able to absorb a significant amount of moisture and, as a result, lose their properties.
If there is a need to perform internal insulation, then it is performed as follows:
- the working surface is carefully prepared, any coating is removed, up to bricks;
- treated with antiseptic agents and ground;
- surface surface;
- strengthen and applied insulation;
- mounted frame for plasterboard or other finish;
- perform the final finish, leaving the gap between the insulation and the layer of finishing.
Also in this case, a number of requirements should be observed:
- necessarily the presence of a vapor barrier layer;
- the thickness of the insulation may exceed the calculated values. But in no case should not be less;
- parosolation of internal insulation requires forced ventilation;
Outdoor insulation
It turned out the spread lately. No regulatory documents including SNiP 23-02-2003 and TSN 23-349-2003 Do not prohibit thermal insulation of structures both outside and from the inside, in the wellwork.
Warm outside
The advantages of outdoor insulation are:
- good thermal insulation;
- withdrawal point dew to the outside of the building;
- preservation of the insulated room;
- the possibility of carrying out work without disturbing the usual rhythm of life inside.
Cons There are also:
- higher price of materials and works;
- changing the appearance of the facade;
- the possibility of work exclusively in the warm season.
In the external placement of the heat insulating layer, the order of work with mineral wool is as follows:
- early brick wall;
- apply glue composition on it;
- anchors fasten the insulation slabs;
- apply a reinforcing composition;
- fix the reinforcing grid;
- apply layer plaster;
- finish insulation in color and facing.
Work with polystyrene foam, stages:
- propinate expanded polystyrene with a special composition;
- additionally fasten it with anchors;
- all angles are closed with a metal corner;
- all joints are watched and put it with a mounting ribbon;
- saw facade layer plaster.
This type of outdoor insulation is used both on the already built buildings and on newly under construction. Installation of the ventilated facade can be carried out in winter.
The order of work is:
- the facade is set by a layer of vaporizolation;
- on top mounted crate of wooden bars or metal profiles;
- in the crate set the heat insulator layer;
- over the insulation lay the windproof layer;
- finds, in the form of lining, siding, facade panels.
Important! Do not save on the quality of the insulation and materials, otherwise then spend much more for heating!
Output
The optimal option is outdoor insulation, but when there is no possibility of external work, you should not neglect internal insulation. All requirements indicated on the materials should be followed in order to get a good effect. In the video presented in this article, you will find additional information on this topic.