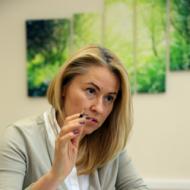
Funzionalità IoT per la manutenzione predittiva. Il progetto "Manutenzione progressiva - APM (Advanced Preventive Maintenance)", realizzato presso lo stabilimento di OJSC "Philip Morris Kuban" Manutenzione preventiva delle apparecchiature
Nel settore industriale della Russia vengono avviati progetti pilota per la manutenzione predittiva. I primi modelli sono già operativi negli impianti metallurgici e nelle unità di potenza delle società di generazione; alla fine del 2017, il volume di mercato è stimato in 100 milioni di dollari.
Attraverso PdM, gli industriali intendono ridurre i tempi di inattività delle apparecchiature e aumentare l'efficienza delle loro strutture. Le tecnologie predittive sono uno degli elementi della digitalizzazione della produzione. Quali aziende sviluppano tecnologie predittive? Quali barriere impediscono al mercato di svilupparsi rapidamente?
Ottimizzazione degli errori
Nel settore, sta guadagnando popolarità un nuovo servizio digitale di "manutenzione predittiva" (manutenzione predittiva, PdM). Il servizio è in fase di implementazione per raccogliere e analizzare le informazioni sullo stato delle apparecchiature, per prevedere i tempi delle riparazioni e prevenire i guasti di produzione.
A differenza della manutenzione preventiva tradizionale, la previsione si basa su array di dati, modelli digitali e non grazie a statistiche medie. Tra i componenti principali di PdM vi sono la raccolta e l'elaborazione delle informazioni correnti, il rilevamento tempestivo di guasti ed errori e l'ottimizzazione delle risorse.
Secondo Markets and Markets, il mercato globale della manutenzione predittiva raggiungerà 1,9 miliardi di dollari nel 2020 (rispetto ai 582 milioni di dollari del 2015). Gli attori chiave nel mondo sono General Electric, Siemens, ABB, Emerson, IBM, SAS, Schneider Electric e altri.
Previsioni del settore
In Russia, l'analisi predittiva è ancora alle posizioni di partenza: secondo le stime degli esperti, il mercato alla fine del 2017 ammontava a 100 milioni di dollari USA, in un anno la cifra potrebbe salire a 200 milioni.Di recente, il settore industriale è stato sempre più utilizzando PdM.
Secondo Konstantin Gorbach, direttore delle applicazioni intelligenti di Zyfra (parte del gruppo Renova), le attività di manutenzione predittiva sono rilevanti per i clienti che utilizzano apparecchiature complesse e costose. Si tratta di industrie in cui il guasto di un elemento provoca perdite significative e minaccia la sicurezza: complesso di combustibili ed energia, metallurgia, petrolchimica, trasporti. Il rilevamento tempestivo dei problemi aiuta a prevenire gli incidenti e a ridurre i costi.
« Il sistema di monitoraggio e previsione a distanza aumenta la trasparenza del funzionamento delle apparecchiature per la gestione”, - ha chiarito il direttore tecnico del sistema di previsione delle condizioni delle apparecchiature PRANA di ROTEK JSC Maxim Lipatov.
Il costo dell'introduzione del PdM nelle imprese si forma in modi diversi: il costo dei progetti pilota può ammontare a diversi milioni di rubli, l'implementazione industriale - da diverse centinaia di milioni.
« Negli ultimi due anni, in Russia è cresciuto l'interesse per l'analisi predittiva. Nel nostro mercato, i principali attori sono ROSTEK con il sistema PRANA, Datadvance, Сlover Group e società di integrazione. Nella nostra pratica c'erano progetti pilota per 10 milioni di rubli e implementazioni industriali per 1 milione di dollari USA”, - ha affermato Sergey Morozov, CEO di Datadvance.
Protezione per un gigawatt
Le società energetiche hanno aderito a PdM nel 2017. Ad esempio, la holding T Plus ha firmato un contratto con ROTEK per l'implementazione del sistema di previsione PRANA a 16 unità di potenza. ROTEK collega le turbine, le caldaie a recupero di calore e i compressori booster della società di generazione al proprio centro situazionale. A causa di questa decisione, la gestione dell'energia prevede di ridurre i costi di riparazione e i tempi di inattività delle apparecchiature, per individuare in anticipo i difetti strutturali nelle apparecchiature.
« Dieci centrali elettriche della società saranno protette dai rischi tecnologici. Questo è il passo più importante verso la digitalizzazione su larga scala del settore energetico: la capacità totale delle apparecchiature collegate al sistema PRANA supererà i 3 GW”, - ha spiegato Mikhail Lifshits, presidente del consiglio di amministrazione di ROTEK.
La tecnologia sta cominciando ad essere utilizzata anche dai gruppi metallurgici. La società di estrazione dell'oro Nordgold ha istituito un sistema di riparazione con l'aiuto di PdM. Tuttavia, alcune pratiche richiedono investimenti e spese per la loro manutenzione in futuro, osserva Alexander Brezhnev, responsabile dell'organizzazione della manutenzione delle attrezzature minerarie presso l'azienda.
Il servizio iniziò ad essere utilizzato presso l'impresa di PJSC Severstal, lo stabilimento metallurgico di Cherepovets. PdM lanciato in produzione per ridurre i tempi di inattività presso il laminatoio a caldo 2000.
« Il modello predittivo rivela la probabilità di surriscaldamento del cuscinetto della gabbia degli ingranaggi, uno dei motivi più frequenti e dispendiosi in termini di risorse per l'arresto dell'unità. Questo è il primo modello nel campo delle riparazioni predittive implementato presso gli impianti di produzione di CherMK come parte dell'implementazione della strategia digitale dell'azienda", - osserva il servizio stampa di Severstal.
Gli specialisti dell'azienda hanno sviluppato un modello digitale per ricevere i dati dai sensori di temperatura e generare una previsione. Se gli indicatori ricevuti dal mulino si discostano dalla norma, l'operatore riceve una notifica corrispondente. Ciò impedisce un arresto imprevisto del mulino.
« Ci aspettiamo che il modello predittivo riduca i tempi di inattività dell'80%. Abbiamo in programma di implementare modelli simili per altri tipi di guasti sul mulino-2000, nonché su altre unità.”, - commenta Sergey Dobrodey, direttore delle riparazioni della Severstal Russian Steel Division.
Effetto economico
Secondo gli esperti, il servizio PdM è ora solo agli inizi nelle regioni della Federazione Russa, i clienti non hanno ancora realizzato il potenziale della direzione.
« L'effetto economico dell'introduzione della manutenzione predittiva può ammontare a centinaia di milioni di rubli, se prendiamo in considerazione Gazprom e le ferrovie russe”, - ha calcolato Alexey Shovkun, direttore della consulenza di Datalytica.
Al momento, notano gli sviluppatori, diverse barriere impediscono la diffusione capillare delle tecnologie. Pertanto, la maggior parte delle apparecchiature in produzione non è dotata di sensori per la trasmissione di informazioni, le imprese non dispongono di sistemi per la raccolta di dati e il monitoraggio online. Inoltre, le fabbriche spesso conservano registri inaffidabili su difetti e riparazioni. L'impreparazione del personale per le soluzioni IT e la sfiducia nel nuovo concetto di servizio ostacolano l'introduzione dei sistemi PdM nelle imprese industriali russe.
L'implementazione della manutenzione preventiva è un passo fondamentale verso l'implementazione del programma di manutenzione predittiva ideale.
La manutenzione preventiva (a volte indicata come manutenzione preventiva) viene regolarmente eseguita su parti di apparecchiature per ridurre la probabilità di guasti alle apparecchiature. La manutenzione preventiva garantisce che le risorse di produzione critiche di un'organizzazione ricevano la manutenzione adeguata per evitare guasti imprevisti e incidenti costosi.
Proprio come cambi l'olio nel motore della tua auto senza aspettare che si guasti, macchine, attrezzature, edifici e altri beni preziosi per la tua organizzazione richiedono una manutenzione costante per evitare interruzioni e costosi incidenti.
Questo lavoro è chiamato manutenzione programmata o preventiva. La manutenzione preventiva viene eseguita mentre l'apparecchiatura sta ancora funzionando normalmente per evitare le conseguenze di guasti imprevisti che comportano un aumento dei costi o tempi di inattività.
La manutenzione preventiva è una strategia che molte aziende possono implementare per abbandonare i regimi di manutenzione reattiva e concentrarsi sul miglioramento dell'affidabilità delle proprie risorse. Poiché i migliori programmi di manutenzione combinano metodi diversi, l'implementazione della manutenzione predittiva è un passo importante verso la realizzazione della strategia di manutenzione predittiva ideale.
Manutenzione preventiva rispetto a reattività
Sebbene molti professionisti stiano perdendo fiducia nel metodo di manutenzione "al fallimento" o reattivo, la maggior parte delle organizzazioni lo utilizza ancora. Manutenzione reattiva significa riparare le apparecchiature solo dopo un guasto e quindi riportarle al normale funzionamento.
A prima vista, la manutenzione reattiva può sembrare meno costosa rispetto ad altri metodi, ma in realtà la manutenzione programmata può essere molto meno costosa. La ricerca mostra che la manutenzione reattiva può costare da cinque a otto volte di più della manutenzione preventiva o predittiva.
Ci sono molti altri costi associati a interruzioni non programmate delle apparecchiature, come prodotti persi, straordinari, apparecchiature non in uso, trasporto urgente e altri costi "nascosti", che possono includere:
- problemi di sicurezza
- spesa di bilancio incontrollata e imprevedibile
- durata ridotta dell'apparecchiatura
- alte possibilità di problemi di controllo
- aumento dei tempi di inattività per attrezzature e dipendenti
- il ripetersi di problemi e fallimenti
Se è pianificata la manutenzione preventiva, questi costi possono essere evitati. Al fine di ottimizzare il processo di manutenzione, tutte le apparecchiature e gli asset dell'azienda possono essere inclusi in un unico programma di manutenzione.
Manutenzione preventiva e manutenzione predittiva
Mentre la manutenzione preventiva viene eseguita secondo programmi basati sulle raccomandazioni del produttore o sul ciclo di vita medio di un asset, la manutenzione predittiva viene condotta su una base molto diversa. La manutenzione predittiva si basa sul monitoraggio dei parametri delle apparecchiature e sulla pianificazione della manutenzione in base a queste letture.
Inoltre, la manutenzione preventiva viene eseguita durante gli arresti programmati delle apparecchiature e la manutenzione preventiva viene eseguita durante il normale funzionamento. La manutenzione predittiva comporta anche l'uso di varie tecnologie avanzate come la termografia a infrarossi, l'analisi delle vibrazioni e l'analisi dell'olio per prevedere i guasti.
I programmi di manutenzione più efficaci utilizzano metodi reattivi, preventivi e predittivi. Pertanto, è necessario analizzare le attività imminenti per determinare quale metodo è migliore, concentrandosi sui tempi di inattività dovuti a guasti delle apparecchiature, periodo di sviluppo del guasto (intervallo P-F - l'intervallo tra guasto potenziale e guasto funzionale), costo delle parti, tempo di funzionamento dell'apparecchiatura e dati sul suo precedente utilizzo.
Come viene eseguita la manutenzione preventiva?
In termini di progettazione e implementazione, un programma di manutenzione preventiva è relativamente semplice. Viene creato un programma di manutenzione basato su un calendario o un tempo di utilizzo dell'apparecchiatura, spesso basato sulle raccomandazioni del produttore. All'ora specificata e per il tempo specificato, l'apparecchiatura viene spenta e gli specialisti della manutenzione eseguono le attività programmate su questa apparecchiatura.
La manutenzione preventiva può anche essere configurata con trigger di manutenzione, controllati in base al tempo o al guasto. I trigger di manutenzione vengono utilizzati per avvisare i dipendenti che la manutenzione deve essere eseguita a livello operativo. I trigger di manutenzione failover si verificano quando un componente dell'apparecchiatura si guasta e non può essere utilizzato fino al completamento della manutenzione. Nel caso di un trigger basato sul tempo, il servizio viene avviato ogni volta che è trascorso il tempo di calendario specificato.
Ad esempio, la maggior parte dei produttori di carrelli elevatori offre una manutenzione preventiva ogni 150-200 ore di funzionamento, che può essere eseguita utilizzando trigger temporizzati. Tale manutenzione prolunga la vita degli asset di produzione, ne aumenta la produttività, migliora l'efficienza complessiva di utilizzo e riduce i costi di manutenzione.
La manutenzione preventiva non richiede strumenti aggiuntivi oltre alle raccomandazioni del produttore e un team che desideri utilizzare nuove procedure di manutenzione. Per far sì che il team lavori con entusiasmo, è importante evidenziare i vantaggi di un programma di manutenzione preventiva e indicare i modi in cui un programma di manutenzione preventiva semplificherà notevolmente il lavoro di tecnici, meccanici e ingegneri.
Mediante un sistema informatico di gestione della manutenzione (CMMS), in una delle aziende è stata effettuata la manutenzione preventiva per controlli periodici basati su date di calendario o orari di funzionamento (per compressori e carrelli elevatori) o in base al chilometraggio per i veicoli. Questa azienda ha aumentato la sua percentuale di manutenzione pianificata dal 20% all'80% e il suo tasso di completamento puntuale per la manutenzione programmata è dell'85% e continua a migliorare.
Strumenti di manutenzione preventiva
Il CMMS è progettato per programmare, pianificare, gestire e tenere traccia delle attività di manutenzione. Le funzionalità CMMS come la creazione di attività, la pianificazione, la convalida e l'integrazione dei dati da strumenti e sensori lavorano insieme per migliorare e supportare continuamente il programma di manutenzione preventiva di un'organizzazione.
- Creare un'attività di manutenzione preventiva. Quando si lavora con il sistema CMMS, gli utenti possono utilizzare il calendario di manutenzione pianificato e/o le attività PM basate sui contatori pianificate per tutte le risorse, nonché descrizioni dettagliate con manuali operativi e altre informazioni vitali per un'esecuzione efficiente del lavoro.
- Programmi per l'esecuzione di attività di manutenzione preventiva. Lo sviluppo di un programma di manutenzione preventiva efficace non riguarda solo la definizione di obiettivi di manutenzione preventiva e i sistemi CMMS dispongono degli strumenti per migliorare significativamente il servizio. I programmi di manutenzione preventiva consentono al personale di coordinare la forza lavoro necessaria per completare il lavoro, nonché di formulare automaticamente le attività di manutenzione preventiva in base alla programmazione giornaliera, settimanale o mensile o in base alle ore di lavoro.
- Ispezioni di manutenzione preventiva. Una soluzione CMMS può anche aiutare le organizzazioni a rispettare i programmi di ispezione e superare gli audit di conformità. Con CMMS, gli utenti possono registrare accuratamente le ispezioni e creare ordini di lavoro correttivi se l'apparecchiatura non supera un'ispezione.
- Strumenti e calibri. In combinazione con il CMMS, il software di monitoraggio delle condizioni consente ai responsabili della manutenzione di monitorare più risorse da remoto. Consente inoltre all'apparecchiatura di generare allarmi e creare più grafici per ciascun asset, mostrando le modifiche di parametri come corrente, tensione, temperatura, livelli di vibrazione e qualità dell'alimentazione.
- Integrazione dei dati. I dati possono essere integrati nel CMMS per consentire processi di produzione senza soluzione di continuità utilizzando dispositivi mobili. Ciò consente ai servizi tecnici di rispondere al volo alle notifiche di guasto e quindi creare, accedere o elaborare gli ordini di lavoro relativi alla notifica in tempo reale. La manutenzione programmata e non programmata viene coordinata meglio, i tempi di inattività non pianificati vengono ridotti ei tempi di risposta a problemi o malfunzionamenti vengono ridotti.
Quali sono i vantaggi della manutenzione preventiva?
Con un efficace programma di manutenzione preventiva, le organizzazioni possono migliorare i loro processi aziendali complessivi, tra cui l'aumento della produttività, la riduzione degli sprechi, l'ottimizzazione delle operazioni e la riduzione delle interruzioni impreviste. Un programma di manutenzione preventiva (supportato da CMMS e altri strumenti) può aiutare a ottenere risultati quantitativi significativi, come:
- Estendere la vita delle risorse di produzione e aumentare il tempo di attività delle apparecchiature
- Ridurre la quantità di dati inseriti manualmente
- Riduci le scartoffie con la funzionalità di servizio mobile
Vantaggi della manutenzione preventiva
A differenza della manutenzione reattiva, la manutenzione preventiva è la strategia di manutenzione più semplice da implementare ed eseguire, in quanto richiede solo il rispetto delle raccomandazioni del produttore e lo sviluppo di programmi di manutenzione statica per le apparecchiature più critiche. Questo aiuta le organizzazioni a evitare interruzioni impreviste, tagli alla produzione e tempi di inattività delle attrezzature e del personale. Riduce anche i costi di manutenzione.
Svantaggi della manutenzione preventiva
Un problema comune che le organizzazioni devono affrontare quando utilizzano programmi di manutenzione preventiva è l'esecuzione di una quantità errata di manutenzione delle risorse. Poiché la manutenzione basata sul calendario non tiene conto dello stato dell'asset, gli intervalli di manutenzione possono spesso essere troppo lunghi o troppo bassi. Questi problemi possono essere prevenuti ottimizzando e migliorando i programmi di manutenzione preventiva.
La manutenzione preventiva ha senso per la tua azienda?
Un servizio di livello mondiale richiede che il 90% del servizio sia programmato, con un rapporto dell'80% programmato contro il 20% non programmato ancora considerato vantaggioso rispetto a una media tipica del 55% o meno. Ma in alcuni casi è più razionale utilizzare un servizio reattivo.
Entrambi i metodi possono essere utilizzati nel piano di manutenzione. In alcuni casi, ha più senso fare affidamento su una manutenzione reattiva piuttosto che seguire un rigoroso programma di manutenzione preventiva. Ad esempio, la sostituzione di una lampadina è poco costosa, facile da eseguire e non interromperà i processi aziendali.
Per determinare quale strategia di manutenzione seguire, considerare le seguenti domande:
- Questa risorsa è fondamentale per il business?
- Dipende dalla sicurezza del tuo prodotto/clienti/personale/ecc.?
- Ci sarà una perdita significativa per l'azienda se l'asset fallisce improvvisamente?
- Quanto sarà costoso riparare o sostituire il bene?
Se hai risposto sì a una di queste domande, è importante iniziare a sviluppare un programma di manutenzione preventiva per quell'asset, poiché ne trarrai vantaggio a lungo termine.
Suggerimenti per lo sviluppo di un piano di manutenzione preventiva
- Creare un elenco di apparecchiature e identificare i migliori candidati per la manutenzione preventiva.
Quando inizi, prendi in considerazione tutte le attrezzature dell'intera organizzazione e includile nell'elenco. Mentre esamini questo elenco, ti porrai le domande di cui sopra per aiutarti a decidere quali apparecchiature includere nel tuo prossimo piano di manutenzione preventiva.
- Fare riferimento alle raccomandazioni del produttore.
Esamina le raccomandazioni del produttore per sviluppare un programma di manutenzione preventiva efficace, determinare cosa è necessario fare e determinare la frequenza di manutenzione desiderata. Tornando all'esempio originale, diciamo che potrebbe cambiare l'olio della tua auto ogni 10.000 miglia o come raccomandato nel manuale del produttore della tua auto.
- Inizia con "influencer".
Per utilizzare in modo efficace un programma di manutenzione preventiva, è necessario iniziare con le apparecchiature più importanti. Dopo aver identificato queste risorse critiche, sviluppa piani a lungo termine come pianificazioni annuali.
- Sviluppare piani a breve termine.
Una volta approvati i piani a lungo termine, puoi iniziare a creare piani settimanali per il team di manutenzione. Questi compiti devono essere assegnati e pianificati con largo anticipo, tenendo conto di tutti i componenti e le risorse da mantenere.
Quando si utilizza un software progettato per la pianificazione della manutenzione predittiva, come CMMS, le organizzazioni ottengono i seguenti vantaggi:
- Prolunga la durata delle risorse e aumenta il tempo di attività delle apparecchiature
- Ridurre la quantità di dati inseriti manualmente
- Riduzione del volume dei documenti cartacei attraverso l'utilizzo di applicazioni mobili e codici a barre
- Semplificazione delle attività e delle procedure di manutenzione
- Aumenta la produttività e l'efficienza
- Migliorare la conformità dei dati di audit con la documentazione esistente
Esempi di utilizzo della manutenzione preventiva
Esistono molte applicazioni per la manutenzione preventiva in un'ampia varietà di settori:
- Esecuzione della manutenzione programmata del condizionatore d'aria nel campus
- Pianificare la manutenzione continua delle risorse critiche per la produzione
- Manutenzione preventiva delle attrezzature per la movimentazione dei materiali, pianificata secondo indicatori misurabili (PM basato sul contatore)
- Pianificazione delle attività di manutenzione preventiva in preparazione degli audit
Articolo tratto da: https://www.accelix.com/community/preventive-maintenance/what-is-preventive-maintenance/
Prova a immaginare di essere in una carriera. È lontano dalla civiltà. Le sue dimensioni sono lunghe due miglia e profonde un miglio. Allo stesso tempo, 45 giganteschi dumper minerari autonomi si trovano ovunque a breve distanza l'uno dall'altro, esportando minerale di ferro.
Ogni ruota di queste macchine è più alta di un essere umano e ogni coppia di pneumatici costa $ 100.000 Questi veicoli operano sotto carichi estremi e in condizioni estreme. È imperativo che lavorino in modo produttivo ogni giorno.
È necessario anticipare i problemi per evitare guasti. Rio Tinto è una società mineraria globale con sede a Londra con importanti sviluppi in Australia e altrove, con la più grande flotta di giganteschi autocarri autonomi al mondo. I suoi dipendenti affrontano questo scenario ogni giorno.
Durante il suo funzionamento, i mezzi dell'azienda hanno trasportato più di 200 milioni di tonnellate di materiali per circa 3,9 milioni di chilometri. Ciò equivale a trasportare circa 5.500 Sydney Harbour Bridge o 540 Empire State Building sulla luna e ritorno cinque volte.
Quindi cosa succede quando una di queste auto si guasta nel bel mezzo di una cava?
Secondo le stime, l'azienda ha perso in media 2 milioni di dollari al giorno per ogni auto ferma. Rimorchiare un autocarro con cassone ribaltabile rotto da una cava spesso costa la stessa cifra: utilizzare un veicolo da lavoro comparabile. Pertanto, le perdite di Rio Tinto sono aumentate da $ 2 milioni a $ 4 milioni al giorno, senza contare la riparazione delle apparecchiature danneggiate.
Mantenere le attrezzature in funzione e ridurre i costi di manutenzione è una sfida costante per qualsiasi azienda mineraria a cielo aperto. Lo stesso vale per qualsiasi altro impianto industriale che richieda un funzionamento continuo.
Risposta: manutenzione preventiva basata su IoT
La manutenzione preventiva basata sull'analisi predittiva consente alle aziende di riparare rapidamente guasti futuri interrompendo il funzionamento dei meccanismi, garantendo la sicurezza. Ciò ti consente di prendere il controllo e portare l'auto fuori dai box utilizzando la potenza rimanente.
L'implementazione della manutenzione preventiva da parte di Rio Tinto ha portato a un enorme ritorno sull'investimento. Proprio come qualsiasi azienda i cui sistemi aziendali e critici affrontano condizioni estreme, le aziende possono beneficiare in modo simile. L'obiettivo di Rio Tinto era aumentare l'efficienza, massimizzare la sicurezza, ridurre il personale e ottimizzare la produzione mettendo in rete processi e attrezzature.
Una parte fondamentale del progetto era automatizzare una flotta di 900 giganteschi autocarri con cassone ribaltabile. Per fare ciò, è stato necessario installare 92 sensori su motori, trasmissioni e ruote su ciascuna vettura.
I sensori monitorano la condizione, la velocità, la posizione e altri parametri. Ciò consente effettivamente ai dumper che viaggiano solo su proprietà private di operare senza conducente e persino di ottimizzare i percorsi per ridurre al minimo il consumo di carburante.
Complessivamente, la flotta di Rio Tinto genera circa 4,9 terabyte di dati al giorno. Queste informazioni vengono utilizzate non solo per controllare il funzionamento del veicolo e migliorare l'efficienza del suo utilizzo.
La manutenzione preventiva aiuta un'azienda a ottenere il massimo da ogni apparecchiatura nel corso della sua vita utile. Ma anche questo piccolo guadagno si aggiunge ad altri grandi vantaggi. Gran parte della tecnologia necessaria per realizzare qualcosa di simile esiste già sotto forma di sensori intelligenti, componenti intelligenti, protocolli di connettività e software forensics.
La manutenzione predittiva abilitata all'IoT per raccogliere e comunicare informazioni sull'hardware dipende da queste risorse. È possibile che il sensore di temperatura rilevi un leggero surriscaldamento del motore. Il sensore di vibrazione è in grado di rilevare vibrazioni oltre i limiti accettabili, indicando un potenziale guasto della ruota.
Il sistema quindi analizza queste informazioni in tempo quasi reale (NRT). Per l'analisi, vengono utilizzati algoritmi e capacità di deep learning per determinare che una particolare parte del meccanismo è usurata e, ad esempio, ha una probabilità del 60% di guasto entro le prossime tre settimane.
Il dipendente responsabile viene avvisato di ordinare rapidamente i ricambi e programmare la manutenzione del veicolo. Con la manutenzione preventiva, risolvi un problema prima che si verifichi, non dopo che ha devastato il tuo programma di produzione.
Quale potrebbe essere la tua corsia preferenziale per il valore dell'IoT?
Operazioni connesse e remote, analisi predittiva e manutenzione predittiva: questi sono quattro percorsi comprovati per il ritorno sull'investimento dell'IoT. I tuoi concorrenti e partner stanno implementando soluzioni IoT in molti settori, dall'agricoltura alla sanità, allo sport e all'intrattenimento.
Maciej Kranz, Vicepresidente dello Strategic Innovation Group di Cisco, lavora con startup e clienti.
Articolo originale: iot-for-all.com
Ognuna delle seguenti cinque strategie di manutenzione delle apparecchiature ha le proprie caratteristiche distintive e applicazioni ottimali.
- Manutenzione preventiva (pianificata) (PM - manutenzione preventiva). Con questa strategia, le attività di manutenzione delle apparecchiature vengono eseguite prima che si verifichi un guasto, quindi non ci sono tempi di fermo delle apparecchiature e il numero di prodotti realizzati non diminuisce. È quasi sempre più economico eseguire la manutenzione programmata piuttosto che attendere un guasto.
- Manutenzione di emergenza (RM - manutenzione reattiva). In questo caso, la manutenzione dell'attrezzatura è una reazione al suo fallimento. Stranamente, a volte questa strategia può essere la migliore, come verrà discusso in seguito.
- Manutenzione predittiva (PdM - manutenzione predittiva). La manutenzione viene eseguita sulla base di informazioni specifiche dell'apparecchiatura, che è un precursore affidabile di guasti imminenti. Gli esempi includono vibrazioni o analisi termica.
- Manutenzione delle condizioni dell'attrezzatura (CBM - manutenzione basata su convenzione). Il termine è talvolta usato come sinonimo di manutenzione programmata. Qual è la differenza? Con la manutenzione programmata, la frequenza delle procedure di manutenzione è impostata in anticipo, in modalità programmata. Nel caso della manutenzione all'avanguardia, il lavoro viene eseguito in base alle informazioni sull'apparecchiatura fornite dai sistemi di raccolta dati in tempo reale, da sensori e altri sensori che misurano determinati parametri. Il sistema di acquisizione dati li correla con i dati specifici della condizione di emergenza in modo che la manutenzione possa essere eseguita prima che l'apparecchiatura si guasti.
- Manutenzione centrata sull'affidabilità (RCM). Copre una vasta gamma di attività e spesso include altre strategie. Il servizio di affidabilità si riferisce al processo di determinazione di un livello minimo di sicurezza del servizio. RCM inizia chiedendoti di rispondere a sette domande sull'hardware:
- Quali caratteristiche e relativi standard prestazionali esistono nella produzione esistente?
- Come si verifica una situazione in cui l'apparecchiatura cessa di svolgere le sue funzioni?
- Quali sono le cause di ciascun tipo di guasto funzionale?
- Cosa succede quando si verifica ogni tipo di errore?
- Qual è il significato di ciascun tipo di guasto?
- Cosa si può fare per prevenire ogni tipo di guasto?
- Cosa devo fare se non riesco a trovare la corretta procedura di manutenzione preventiva?
RCM è un approccio ingegneristico completo che mira a eseguire tutto il lavoro necessario per garantire il massimo livello di affidabilità delle apparecchiature, riducendo al minimo i costi di manutenzione.
Come scegliere la giusta strategia
Manutenzione preventiva (pianificata).
Per mantenere la tua attrezzatura in funzione, devi sviluppare piani di lavoro dettagliati che specifichino tutte le attività di manutenzione per l'attrezzatura e gli intervalli di tempo per ciascuna di tali attività. Avrai anche bisogno di un sistema per raccogliere informazioni sulle condizioni dell'attrezzatura, che verranno accumulate durante le ispezioni. Questo di solito viene fatto emettendo attività di manutenzione programmata e i dati per ulteriori analisi vengono raccolti da un sistema di gestione della manutenzione computerizzato (MMS - sistema di gestione della manutenzione).
servizio di emergenza
È la strategia giusta solo se non esiste un modo semplice ed economico per riparare l'attrezzatura. Se è più economico sostituire una parte piuttosto che ripararla, è necessario utilizzare una strategia di servizio di emergenza e mantenere uno stock costante di parti di ricambio. Un esempio di tale parte è un motore elettrico con una potenza inferiore a 5 CV.
manutenzione predittiva
Per fornire tali servizi, è necessario spendere soldi per l'acquisto di apparecchiature analitiche e formazione degli utenti o per il coinvolgimento di appaltatori per eseguire l'analisi. La scelta giusta dipenderà dalla situazione specifica.
Servizio in base alle condizioni dell'attrezzatura
In generale, questa è una buona strategia (ovviamente, a seconda della tua attrezzatura), ed è anche un buon modo per risparmiare sullo sforzo investito. Il CBM di solito richiede investimenti in un sistema di raccolta dati remoto e formazione degli utenti.
Servizio Affidabilità
Nel complesso un'eccellente strategia di manutenzione ed è considerata da molti esperti la più conveniente. Come accennato in precedenza, RCM può coprire tutte le altre strategie a seconda dei componenti hardware e delle risorse disponibili.
Foto scattata qui: http://xcompstore.pl/uslugi/.
Chi potrebbe essere interessato
PdM (manutenzione predittiva, manutenzione predittiva) è un tipo di manutenzione delle apparecchiature basata sulla diagnostica e sul monitoraggio delle sue condizioni.
L'approccio moderno alla manutenzione delle apparecchiature si basa sulla metodologia, secondo la quale lo scopo della manutenzione non è mantenere ogni singola apparecchiatura in perfette condizioni (il che richiede costi irragionevolmente elevati), ma garantire l'affidabilità dei processi produttivi e tecnologici che sono fondamentale per l'impresa. Allo stesso tempo, i tipi tradizionali di manutenzione possono essere utilizzati per apparecchiature non critiche:
- Reattivo - MTBF senza manutenzione; utilizzato quando le apparecchiature possono essere facilmente sostituite o riparate senza influire sulle operazioni aziendali
- Preventivo - simile al sistema di manutenzione preventiva (PPR); utilizzato per apparecchiature in cui i costi di fermo macchina sono bassi e la riparazione è breve
Manutenzione predittiva (predittiva). viene utilizzato nei casi in cui il grado di utilizzo delle apparecchiature nella catena di produzione è valutato elevato e il suo guasto o lunghi tempi di inattività comportano perdite finanziarie significative.
La manutenzione predittiva, a differenza della manutenzione preventiva, consente di effettuare le riparazioni non secondo un piano prestabilito, ma quando se ne presenta la necessità. Grazie a ciò, da un lato, è possibile non spendere tempo e denaro per la manutenzione programmata di apparecchiature che possono funzionare normalmente per diversi mesi senza riparazioni, dall'altro la probabilità di tempi di inattività non pianificati causati da un guasto imprevisto è ridotta ridotto.
Ciò si ottiene attraverso:
- raccolta di dati sulle condizioni tecniche delle apparecchiature e loro elaborazione preliminare
- rilevamento precoce dei guasti
- previsione del tempo di guasto
- pianificazione del servizio
- ottimizzazione delle risorse destinate alla manutenzione delle apparecchiature
Man mano che i mezzi (IIoT) si sviluppano, in particolare, grazie all'equipaggiamento dell'apparecchiatura con vari sensori, la raccolta di dati sulle sue condizioni tecniche può essere eseguita non periodicamente, ma continuamente, senza interrompere il funzionamento dell'apparecchiatura. Il rilevamento tempestivo anche di piccole deviazioni nei parametri operativi consentirà di adottare rapidamente misure per garantire il normale funzionamento dell'apparecchiatura. Le tecnologie (Big Data) consentiranno di prevedere il momento del guasto con elevata precisione.
I principali vantaggi del sistema PdM:
- efficienza nella pianificazione del servizio
- prevenire guasti imprevisti
Sapere quali apparecchiature necessitano di manutenzione può essere programmato per il periodo in cui sarà più conveniente. In questo modo, lunghi tempi di inattività non pianificati vengono convertiti in tempi di inattività pianificati più brevi e il tempo di disponibilità delle apparecchiature aumenta.
Altri potenziali vantaggi del PdM:
- aumentare la durata delle apparecchiature
- miglioramento della sicurezza della produzione
- riduzione del numero di incidenti con impatto negativo sull'ambiente
- formazione di un set ottimale di pezzi di ricambio e materiali
Nel sistema IT-Enterprise, la manutenzione predittiva è fornita dal prodotto "". Fornisce un alto livello di affidabilità per ogni apparecchiatura.